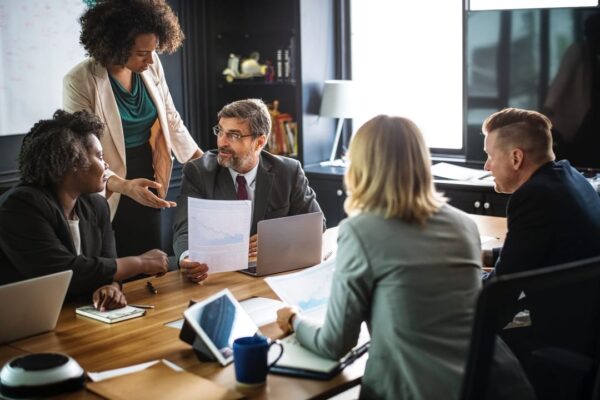
We all make mistakes, but repeatedly making the same mistakes over and over again with your business can cost you time and money, and can stop clients from knocking at your door.
Read on to learn about 5 common mistakes that businesses make and how ERPs can solve them.
1. Duplicating information
This is a big time waster for lots of manufacturing businesses. Instead of keeping information in one centralized and connected system, various spreadsheets and business systems are used to manage your corporate data. This means that your staff is constantly entering the same information into different spreadsheets and systems. Not only is this a major time-waster, eating up time your staff could be doing more productive tasks, but it is also an easy way errors can creep into your data. Simple typos and human errors will inevitably occur during data entry, and by constantly re-entering the same information, you’re creating greater chances for errors to be made — and more chances for errors to compounded, as simple typos can be reproduced over and over again.
Another way this type of record keeping hurts manufacturing businesses is not having one single source of truth. If you are using multiple spreadsheets and systems to keep track of your information, which one is accurate?
By using and ERP you gain one centralized and connected system for all of your corporate data and information. You will stop wasting precious time re-entering information into various systems, and your entire operation will run off of the same data set. Instead of re-entering the same information into their various systems, your data only has to be input once, saving staff time. You also have a single source of truth for your information, and as long as you have proper controls in place, your whole operation will be working from the same accurate data. What does this mean for you? Your team is now free to concentrate on more important tasks, ones that are likely to have a bigger impact on your business.
2. Not keeping track of your business resources
You need your shop to be running at maximum capacity of you want to be profitable and competitive. But if you don’t have a handle on your business resources — what your business has in terms of cash, raw materials, personnel, and production capacity — you’ll have a hard time running at full capacity and maximizing your throughput.
With no overarching system that collects data, reports on your processes and systems, and sees the big picture how can you accurately know where you stand? Your business resources are what you use to keep your business running, and you should be aware of where you stand at all times.
One of the greatest aspects of ERPs is their ability to provide comprehensive visibility. An ERP gives you an overarching view of your operations, letting you know how every aspect of your operation is performing, including your shop floor. An ERP can give you production statistics, like staff productivity and machining time. And with an ERP what used to take hours of meticulous data collection, and report creation, can be done automatically giving you a comprehensive overview of your operation. You can use this information to optimize production schedules, equipment and labor — to maximize capacity and increase your throughput.
3. Not using real-time data to manage operations
Real-time data is probably something you hear over and over again from ERP providers, but it really is important. If you are running your shop on data that isn’t accurate and up-to-date, you will always be behind the eight ball, so to speak. Knowing which production processes, machines, work centers and product lines are operating at high-quality levels and which aren’t is essential for keeping shop floor operations running smoothly. Having real-time data for continually tracking, controlling and fine-tuning manufacturing processes is key.
ERPs give you just that advantage — they let you see how your data and how your system is running in real-time. Real-time data lets you know how your shop is actually functioning, and can alert you to a problem or bottleneck on your line, and let you sort it out quickly on the spot. Real-time data can also help you schedule your shop more efficiently, and give you a better estimate of how long a job will actually take your shop to do, making you better equipped to provide an accurate timeline to your customer, and to then deliver on time — leaving you with much happier customers.
4. Poor customer service
Let’s face it, your customers are everything. Without happy and satisfied customers your shop can’t exist. You need to keep your customers happy, and keep them coming back to you, to stay in business. A poor customer experience, and poor customer service, can be major roadblocks to your business success.
How exactly can an ERP help you deliver a better customer experience you may ask? Well for one, we’ve already seen how an ERP can help you give your customers more accurate quotes and timelines, and then deliver on time, making your customers happier, and more likely to use you again for another job. Accurate production planning, enhanced control over inventory, streamlined process scheduling, and coordination of distribution channels enable manufacturers to improve on-time delivery of products are not just critical performance metrics that ERPs help improve. Delivering products on time is critical to maintaining good customer satisfaction.
A good ERP will also include a CRM or Customer Relationship Management function, that lets you keep all of your records and interactions with a customer in one place. You’ll be more organized and able to know the status of each job you have for a customer. You’ll also be able to handle customer questions and inquiries, faster and easier, and provide your customers with quicker and better answers, enhancing your customer service and your relationships with your customers.
5. Not collaborating
Collaboration isn’t just a buzzword that your millenial staff members like to throw around. Being able to work well with others is a crucial part of doing business. This means that you need to work well with others outside of your company — suppliers, vendors, customers, subcontractors — but that your staff also has to communicate and share information to get their jobs done efficiently and effectively.
ERPs can help on both fronts. ERPs have vendor management and customer relationship management functions that let you be more organized, and communicate more easily with partners. You’ll always know where you stand and what you need, or need to deliver, to keep your business running smoothly, — and with an ERP you’ll always know what you need to ask for to get the job done.
And we’ve already talked about how a centralized database is an integral part of what makes an ERP unique. With this database, you provide your company with a single source of truth to work from. This reduces any errors brought on by working with the incorrect data, further reducing costs. You also make it easier for your staff to work together and share information. Your engineering department won’t have to wait for information from your sales staff to get a job rolling — data will already be input into the ERP making it easier for your team to get their jobs done.
To build a sustainable and profitable manufacturing business you need to stop making common business mistakes, and start using tools that help you streamline tasks, boost productivity, and leverage data in real-time. The right ERP system can put you on the right track to success.
Get your eBook Scared to implement a new ERP?
"*" indicates required fields