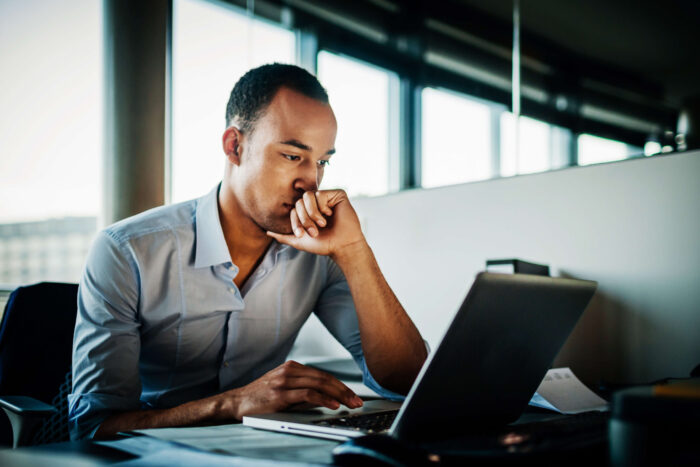
How using an ERP could lead to more efficient purchasing
Keeping on top of purchasing requests, managing inventory levels, and trying to negotiate with vendors can make even the best purchasing manager feel like they live in a constant state of chaos. Custom manufacturing involves a lot of moving parts (literally)—and the purchasing department is responsible for ensuring all these parts are in the right place at the right time.
Sometimes it’s easy to forget that among all of the features your ERP has to offer, an ERP can also help streamline the purchasing process, by ensuring you always have the right level of stock on hand, and help you handle the intricacies of low-mix, high-variable manufacturing. An ERP will ease supplier management by making the procurement process smoother, giving you more time to focus on other areas, and a more efficient business.
Better management of purchase orders
Think about the hours and effort that go into purchasing: creating tracking numbers, filing orders, checking inventory, making a purchase history, coordinating with suppliers, and so on. An ERP makes purchasing easier by automating these tasks, and providing you with accurate real-time data. Because an ERP is always managing your inventory levels in the background of everything you do, you will know what stock you have on hand, and what needs to be ordered to complete a job. You will also be able to create a PO with one click—saving you time and streamlining the purchasing process.
An ERP will also help you oversee your purchase orders, by breaking down orders so that they can include specific lines that refer to specific items, and they can allow for multiple delivery dates to be specified. You will be better able to keep track of which parts are required for which jobs, and have a more organized purchase ordering system. With an ERP you will also increase the negotiating power of your purchasing department by aggregating POs, giving you more power to negotiate with vendors, and ultimately saving you money.
Optimized supplier relationship management
Managing your relationships with suppliers is one of the biggest tasks a purchasing department is required to do. Using an ERP can help you create better relationships and enhance and streamline communications with suppliers.
An ERP system will allow you to create a robust supplier database—essential to all manufacturers that order multiple parts from multiple suppliers. From names and addresses to parts and materials offered and tax identification data, your ERP collects and organizes all the supplier information you’ll need. You will always be confident that you have the right information about your suppliers, making it easier to submit requests and orders.
Using an ERP to handle your supplier communications will also streamline the process: By using a purchasing portal that is fully integrated with your current jobs and existing inventory, you can make simultaneous pricing inquiries for multiple items to multiple suppliers, and receive prices from suppliers without having to re-enter any information. Using an ERP for inventory control also gives you a basis for more open communications, allowing you to offer suppliers better lead times, earlier warnings for quantity adjustments, and more reliable predictive modelling. This not only improve resource planning on your end, but undoubtedly helps build supplier respect.
Good supplier relationships require a level of transparency. A fully integrated ERP software system will balance your sales demands, buying processes, and inventory controls with the capabilities and capacities of your suppliers. This makes for more transparent dealings, and encourages a better understanding of both parties’ business needs, helping you to create better and more open relationships with your suppliers.
Time savings and improved productivity
With an ERP you will streamline and automate many of the purchasing tasks and processes making you a more productive organization.
Improving and automating processes saves time, increases productivity and improves relationships. For example, automating inventory management with an ERP helps keep stock at the right levels, and alerts your purchasing department when the stock reaches a certain level, notifying you that stock needs to be reordered—or can even automatically re-order the stock for you.
Increased productivity means better utilisation of resources, cost-savings and potential business growth. The right ERP system can put you on the right track to success, and give you the tools you need to help you streamline tasks, boost productivity, and leverage data in real-time.
How Genius ERP can improve your purchasing processes
Genius ERP helps purchasing managers and departments stay organized and ahead of the chaos. Genius is designed specifically for manufacturers and understands the complexities of the CTO and ETO manufacturing environment. Genius ERP includes all the features that a purchasing department needs: One-click PO creation; an integrated supplier database, the ability to aggregate POs to increase the negotiating power of your purchasing department; and all the data, information and tools you need to ensure that you are using the best vendors for the job, in terms of value, on-time delivery, quality and cost.
Genius ERP’s CAD2BOM feature will automatically generate a checklist of what needs to be purchased, in what quantities, and when items are needed, giving purchasers more time to focus on negotiations, networking, vendor evaluation, and buying strategy. This feature is especially useful for the procurement on long-lead items, giving the purchasing department more time track down these items during the design-phase of a job.
Genius ERP will also help you to avoid interruptions to jobs with Genius Vendors, a purchasing portal that syncs with your current jobs and existing inventory. You can make pricing inquiries for multiple items to multiple suppliers at the same time, and receive prices from suppliers without having to re-enter any information, saving time and letting you pick the best supplier for the job.
The recommended repurchasing function in Genius Vendors will identify potential shortages based on real-time inventory, expected delivery times, and the date required for the item according to in-process production orders. Genius Vendors also allows you to reorder items based on minimum stock or to combine purchase lists from multiple orders.
Genius Inventory Management lets you track by serial number and associate different statuses to materials, so that specific materials can be counted and allocated before production begins. Purchasing managers will always be in the know—knowing which parts are already on hand and what parts need to be ordered to complete a job.
Better inventory tracking, and the ability to assign parts to jobs, makes the purchasing process more streamlined and organized. You will avoid production interruptions by eliminating surprise material shortages and replenish based on actual on-the-job demand or for inventory. And you can use mobile devices to move material, manage inventory, and eliminate duplicate data entry.
To discuss more ways that Genius ERP can improve the purchasing process and build better supplier relationships and processes.
Get your eBook Scared to implement a new ERP?
"*" indicates required fields