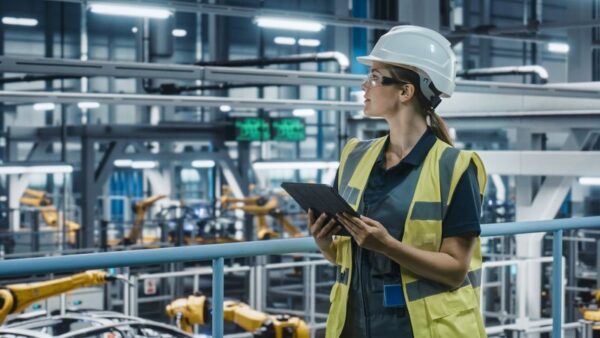
Industry 4.0 is the combination of innovations in digital technologies that are changing the face of the manufacturing industry. Widespread adoption of new processes and technologies such as big data, artificial intelligence, the internet of things (IoT), sophisticated sensors, 3D printing, and other digital applications and technologies are changing how manufacturers do business.
The manufacturing industry is constantly undergoing change with the advancement of new technologies that push the industry forward. These changes can be roughly grouped into four major eras:
Industry 4.0, building upon the automation and computerization of Industry 3.0, is causing a huge upheaval for manufacturers, and those who do not embrace new ways of doing business may see themselves lag behind their competitors.
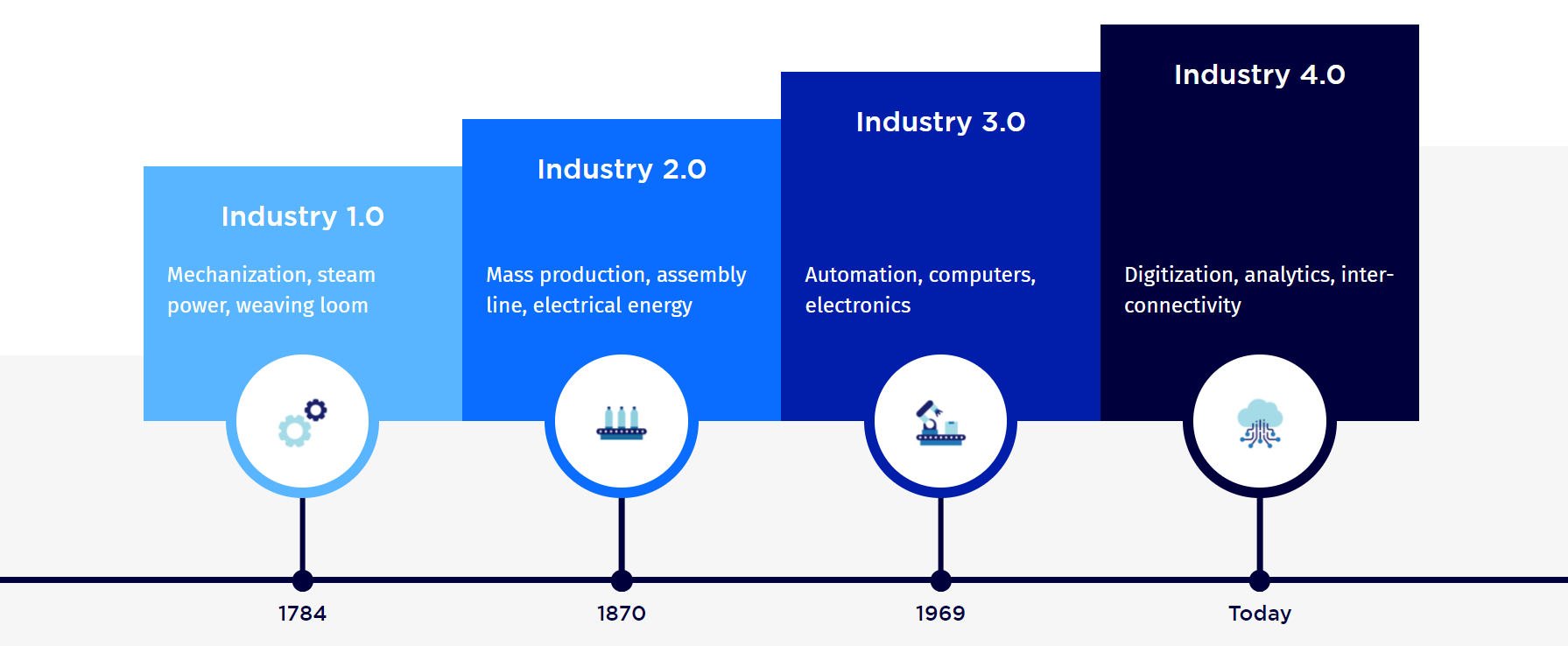
Industries Affected by Industry 4.0
All manufacturers have been affected by Industry 4.0, with new technologies changing how they do business, including custom manufacturers.
Henry Ford may have once famously said: “Any customer can have a car painted any color that he wants so long as it is black.” But custom manufacturers have long known that this attitude doesn’t cut it. Custom manufacturers need to create unique products that meet their customers’ wants and needs while striving to balance profitability and productivity.
Industry 4.0 has opened up new possibilities and opportunities for custom manufacturers to successfully create, design, and manufacture custom products while maintaining efficiency and profitability.
Smart production lines that rely on real-time data can help custom manufacturers quickly and easily change the type of product being produced. Other technologies, like 3D printing, can help speed up the design and prototyping phases. These are just a couple of examples of how Industry 4.0 technologies can make custom manufacturers more productive.
How Does Industry 4.0 Affect Manufacturing?
Data Analytics
One of the easiest ways manufacturers can improve efficiency is by implementing data analytics. Data that is correctly gathered, processed, and analyzed is a treasure trove for manufacturers. It can be used for everything from predictive equipment maintenance to aligning shop priorities and creating more accurate schedules. Learn more about data analytics here.
Automated Production Lines
Automated production lines allow manufacturers to reconfigure their lines quickly, making it easier for them to adjust product specs or switch between product types — a considerable benefit to custom manufacturers. This allows for continuous production of variable mixtures of products and gives custom manufacturers the flexibility they need.
Additive Manufacturing
Industry 4.0 technologies like 3D printing can help manufacturers – including custom manufacturers — reduce R&D expenses. 3D printing can help manufacturers create prototypes and models of working products to test any hypotheses quickly. 3D printing can lower costs and speed up the design process, making manufacturers more efficient.
Paperless 4.0
Using paper to manage your shop is both costly and time-consuming. A connected shop floor empowers both workers and management by connecting them with the information they need to do their jobs. Moving from sticky notes and spreadsheets to integrated shop floor management software is one of the first steps manufacturers can take to create the seamless integrations and streamlined processes of Industry 4.0.
Smart Sensors
Implementing sensor technology throughout your plant or shop can help you do things like effectively manage your inventory by guaranteeing that counts are accurate and parts are easily locatable. Smart sensors can also detect vibrations in a piece of machinery, alerting you to issues before they become major problems. Sensors can help you eliminate downtime and improve quality by keeping an eye on everything on your shop floor.
Asynchronous Manufacturing
Traditional manufacturing assembly lines are synchronous, with predefined workflows. Industry 4.0 technology allows for asynchronous assembly lines that use new flexible machines that adapt to the requirements for the part being made. Components in the production flow use auto-identification technology to inform each machine and operator what needs to be done to produce the customized end product at each step of the production process. This creates a more agile and efficient production line — making it easier to manufacture custom products efficiently and profitably.
Get Your Shop Ready for Industry 4.0
The possibilities of Industry 4.0 are exciting, but it is daunting to think of how to get your shop ready to embrace all of this new technology.
The best place to start is with an ERP system. While ERPs have been around for decades, they have never been more relevant than they are today, as they are the foundation of Industry 4.0 for manufacturers.
ERPs are the best way to create visibility and connectivity across your organization to increase efficiency, improve business processes, and lower your operational costs.
Without an ERP system, you will need to run their organization using multiple software programs and systems, like Excel, that do not talk to or work with each other. This results in poor performance by limiting connectivity, slowing down collaboration, and hindering productivity.
ERPs also supply manufacturers with real-time data, which opens up countless possibilities.
Data is one of the key drivers behind Industry 4.0. If manufacturers learn how to harness the real-time data that they already have coming from their ERPs, they will not only immediately become more efficient — they will also be on the right path to embracing the connected technology of Industry 4.0.
An ERP is the best solution for integrating people, processes, and technologies across a business — making manufacturers ready for Industry 4.0.
To learn more about how to get your business ready, watch our webinar: Get Your Business Ready for Manufacturing 4.0.
Get your eBook Scared to implement a new ERP?
"*" indicates required fields