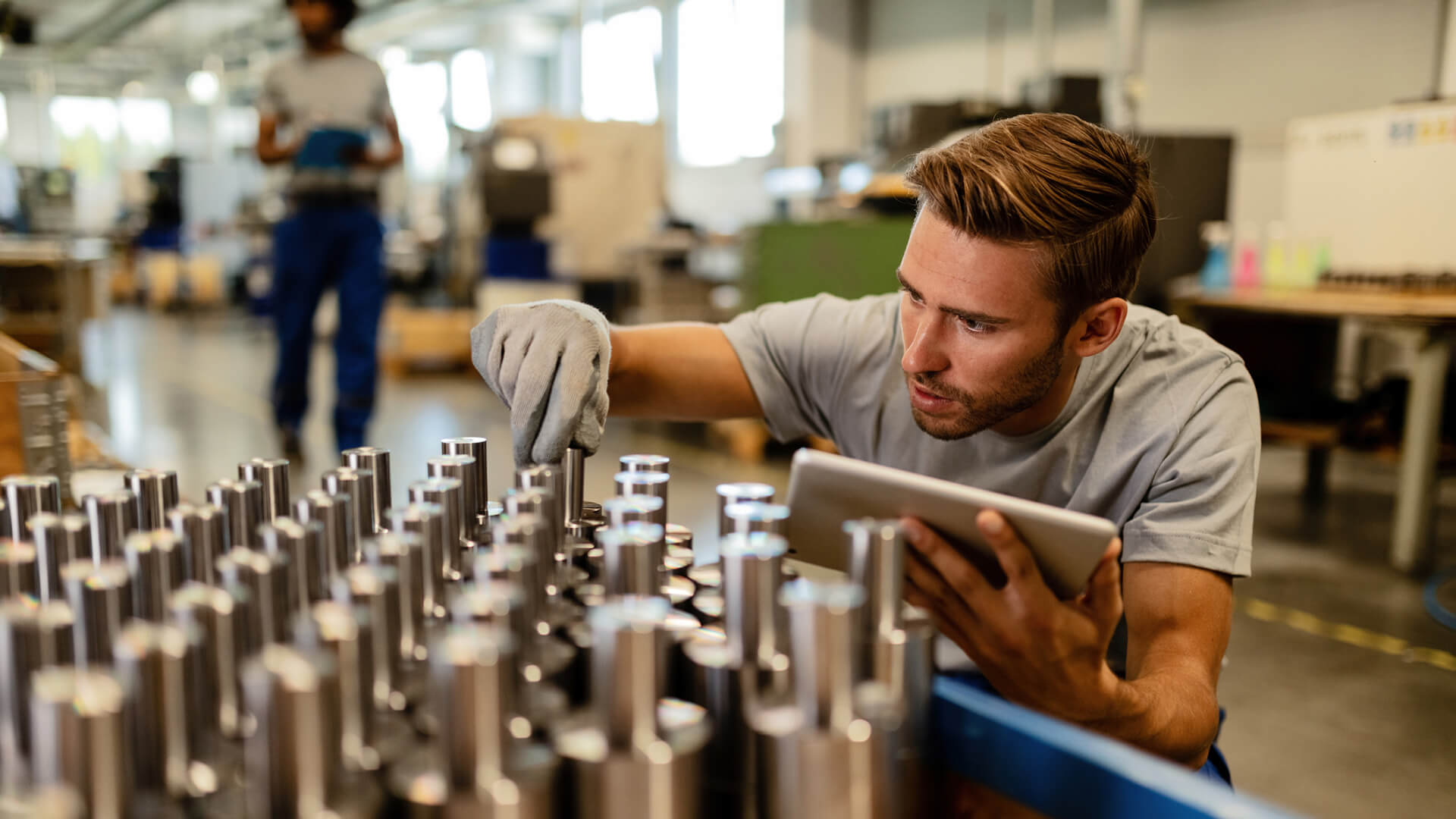
What Is Quality Management?
Quality management involves overseeing all activities and tasks that must be accomplished to maintain the desired level of quality within your shop. Quality management includes creating and implementing quality planning and assurance, as well as quality control and quality improvement.
Why Is Quality Management Important?
The long-term success of your business depends on customer loyalty and satisfaction. Along with on-time delivery, product quality is the top factor that your customers will judge you on. It is imperative that you consistently deliver high-quality products to your customers in order to retain their business.
Implementing good quality management practices is a must for all custom manufacturers to ensure a high level of quality. Companies that regularly deliver high-quality products have the best chance of winning their customers’ trust and satisfaction. High levels of quality lead to repeat business, increased profits, and recognition within your industry — plus, implementing good quality management practices will also increase your business’s efficiency and lower costs by reducing waste.
5 Ways To Improve Your Quality Management
1. Keep your shop clean.
One of the simplest ways to improve quality in your shop is to keep your shop clean.
Not only does a tidy shop improve worker safety, but it is also a simple and effective way to keep your shop running smoothly and efficiently, reducing errors and mistakes, which will improve quality.
You must set clear guidelines for shop floor cleanliness and put time aside time to tidy your shop. To ensure workers maintain a clean shop floor, implement the ‘Pick Up As You Go’ technique to get your employees in the habit of tidying up after themselves. Ensure you always clean up unexpected messes to keep your shop in good condition.
It may sound simple, but a tidy shop really is an effective way of increasing quality in your shop.
2. Define your quality standards.
Before your shop can deliver quality goods, you need to set your quality standards. To do so, first answer this question: How will you define quality in your plant? Your response to this question will be your jumping-off point for setting up and implementing quality management procedures in your shop.
You will need to consider the number of defects you are willing to tolerate, the processes you want to optimize, and the quality targets you want to achieve. Setting clear standards and goals is a must before you can implement effective quality management practices.
Also, take a little time to decide when you will assess quality — some shops opt for end-product evaluations, but many find it better and more efficient to monitor quality throughout the production process.
3. Have a quality management system.
The most important factor in creating quality products. Modern manufacturing is just too complicated to go without one.
A quality management system is the collection of processes, procedures, and practices that a business uses to create quality goods that consistently meet customer requirements and enhance their satisfaction.
Like with many other areas within custom manufacturing, the easiest way for manufacturers to keep on top of quality in their shops is to use their ERP system. Manufacturing-specific ERP systems are designed to meet the unique needs of custom manufacturers and have built-in quality control features to help custom manufacturers consistently create high-quality products. ERPs let you set up, manage, and track quality control from one integrated system.
An ERP will handle many aspects of quality for a manufacturing company, including compliance, quality audits, corrective and preventive actions (CAPA), regulations, and approvals.
4. Make quality a part of your company culture.
If you don’t make quality an integral part of your company’s culture, you will find it hard to get your employees to focus on it.
All employees across your shop must be committed to quality — not just your quality management officer. Train everyone in your shop to asses processes for quality and to keep an eye out for defects. Plus, you should empower your staff to make suggestions for enhancing productivity and quality control in your shop.
Keep in mind that quality control often suffers the most during times of change — which is pretty much a given in the complex world of custom manufacturing. With more of your staff focused on quality, your business will have extra eyes on the floor to notice problems before the issues evolve into faulty products.
5. Use technology to help.
A QMS system integrated with your ERP is the most important technology you can use in your shop to ensure that you deliver consistent quality products.
But other technologies can help too.
Don’t overlook how technology can increase your shop’s efficiency and quality control. Data collection is a crucial component of quality management, and depending on your operations, various technologies are available on the market that can help you increase quality.
To track products, for instance, you can install real-time sensors that are connected to software that can notify you as soon as a defect is found. This will enable you to halt the product — and fix the problem — before it moves along the assembly line or is shipped out to a customer.
Conclusion
Quality management should never be an afterthought.
Delivering quality products is one of the most important things your shop can do to increase customer satisfaction — and secure the long-term viability of your business. Though establishing quality management processes may take some time, they ultimately save you time and money and will help you improve customer loyalty and satisfaction.
Get your eBook Scared to implement a new ERP?
"*" indicates required fields