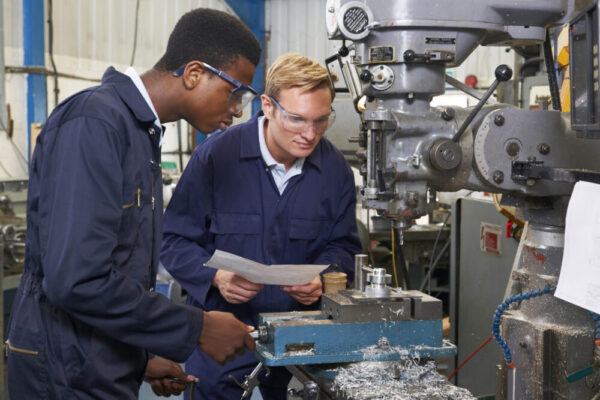
Labor costs are one of the biggest line items in your budget as a manufacturer, so keeping them under control is key to being profitable.
But staying on top of labor costs, tracking where your employees are spending time, and identifying efficiencies to save on labor can be difficult and time-consuming. And if you are using pen and paper, or even an Excel spreadsheet to manage your labor costs, you are probably both spending too much time doing it, and doing an inefficient job of it. Manually tracking your labor can slow down the day-to-day operations of your business, and take you longer to balance your job tasks. You may find that you have employees standing around idle waiting for you to tell them what to do, or what job to move on to next — and then they may still be waiting for detailed instructions from you before they can start their next project.
Take Control of Labor Costs with an ERP
To better manage labor costs, you need to better manage your shop — meaning you need a more efficient and automated way to allocate time and resources. One of the best ways to get on top of your labor costs is to use an ERP system. An ERP can help you on so many different levels — from providing you with real-time data, to help you create better schedules, to optimizing your production — which will make you more productive and efficient, helping you to keep your labor costs under control.
Using an ERP will provide you with real-time data from your shop floor, giving you more visibility into how your staff is spending their time, and where bottlenecks are occurring on your shop floor that prevent your employees from efficiently doing their jobs. ERPs will also let your employees log in and out of jobs, and let you see job sequences, so you will always know how a job is progressing — letting you take action if things are moving along too slow. And all of this information can be delivered directly to your desktop through custom dashboards, meaning you don’t have to walk the shop floor to know what is going on — you will always have the information you need to take action and help your shop run more smoothly at your fingertips.
Moving away from a paper-based system to track labor costs will also eliminate the likelihood of important information like timesheets being lost, as a paperless system will save this data for you. You will also be able to track your direct labor time down to the minute, for each and every job that your team works on.
Optimize Production, Lower Labor Costs
The biggest cost savings an ERP can bring you is by helping you to streamline your production, making you more efficient — which will help you lower your labor costs. An ERP can automate processes, making your entire line more efficient, and your employees more productive. For example, when was the last time you reviewed your processes or your shop layout to maximize productivity? Armed with the data an ERP provides you about your entire shop, you can redesign your manufacturing processes or shop layout to create a more lean, more effective manufacturing environment.
Using historical data, and the actual capacity of your shop floor, you will be able to schedule both machine time and labor more accurately meaning less time that your employees are standing around waiting for a new task to work on, or waiting for instructions. When you don’t have access to shop floor data, your scheduling to some degree is just your best guess. But by using an ERP, predictive scheduling software can use this data to create an optimized labor schedule. You will also be able to look ahead at the incoming production demand and make scheduling decisions using that data. This ensures that your shop is adequately staffed to meet the demand and eliminates excessive/unnecessary labor hours.
And an ERP can help you identify and eliminate non-value added processes within your manufacturing, which can help you increase labor productivity and cut production throughput times. With a more efficient production process, employees are able to produce more products — thus lowering your labor cost per unit, and your overall labor costs. An ERP can also help you keep on top of your shop in other ways, for example, by creating a preventative maintenance schedule for you. By having better-scheduled maintenance you will have a shop that is always running smoothly and won’t get caught out when a crucial piece of equipment conks out, grinding your operation to a halt, and leaving your employees with nothing to do.
Cost Reduction by Design
Another way to lower your labor cost is to design a better product. Product development drives around 80 percent of the product’s cost, and of that cost, the concept and program architecture drive about 60 percent. Therefore, manufacturers can save a significant amount of money on parts, materials, quality and labor by considering cost reduction during the design phase of the product.
But how can an ERP help with that, you might be asking. An ERP that automatically connects your CAD program to your ERP, allowing for information, like BOMs and routing instructions, to be transferred at a click of a button, saves your engineering department significant amounts of time. By reducing the amount of time your engineering department spends on data entry and double checking that information from your CAD software has been transferred correctly, you free up time for your engineering department to spend on what they do best — designing and engineering products. By using an ERP to help streamline and automate processes, you give your staff time to do their jobs better. Maybe your engineering department will spend the same amount of hours on a job, but instead of a large portion of that time being used up by data entry, they will have more time to design a better product — one that can save you time and money all the way down the production line.
An ERP can help your shop do a lot of things more efficiently, which in the end will help you to lower your labor costs. Your skilled workforce is one of your biggest assets as a company, so learning to manage them more effectively will keep your staff happy and your labor costs in check.
Get your eBook Scared to implement a new ERP?
"*" indicates required fields