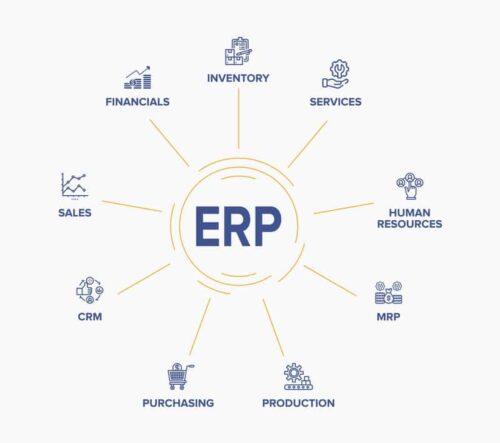
ERP stands for Enterprise Resource Planning — but what does that actually mean?
An ERP is business process management software that connects and integrates every aspect of a business — giving manufacturers visibility over their entire operation and allowing them to create better manufacturing processes, lower costs, and improve performance.
Without an ERP system, manufacturers need to use multiple software programs and systems, like Excel, that don’t talk or work with each other to run their organization. This results in poor performance by slowing down collaboration and limiting efficiency.
An ERP system integrates a company’s financials, supply chain, operations, reporting, and manufacturing activities into one system, helping manufacturers increase productivity and lower costs.
History of ERP Systems
The term ERP was coined in the 1990s, but enterprise resource planning systems actually have their roots deep in the manufacturing industry and can trace their history back to the 1960s.
During the 60s, basic software solutions known as MRPs or Material Requirements Planning systems were developed to help manufacturers manage, track, and control their inventory. These systems helped manufacturers monitor inventory, reconcile balances, as well as included very basic manufacturing, purchasing, and delivery functions.
Through the 1970s, more and more manufacturers started to adopt MRP systems, and the systems themselves got more sophisticated. By the 1980s, MRP systems evolved into what became known as MRP II or Manufacturing Resource Planning systems. Additional manufacturing processes were added into the original systems, and MRP II systems had expanded capabilities and were better able to handle scheduling and production processes.
In the 1990s, the first true ERP systems came into use when other functions, such as accounting, finance, and sales, were added into MRP II systems. These systems set the stage for ERP solutions as we’ve come to know them today by integrating multiple processes and departments into one system.
ERPs in the Modern Manufacturing World
Modern ERP systems connect every department and aspect of your business — but can do so much more.
The ERP systems found on the market today are extremely flexible and offer a variety of tools, features, and functionalities designed to meet the unique needs and challenges of different industries.
Modern ERP solutions not only include manufacturing, supply chain management, and financial and accounting capabilities, but they also can have advanced reporting and business intelligence, sales force and marketing automation, CRM management, and project management functionalities.
How Does an ERP Work?
ERPs run your organization off of a single, shared database to tie together all of your business processes and enable the flow of data between them. This means that the information used across your organization is normalized and standardized.
Instead of several standalone databases with an endless amount of disconnected spreadsheets, ERP systems bring order to chaos so that all users — from the CEO to shop-floor staff — can create, store, and use the same data derived through common processes. Not only does this mean that ERPs eliminate data duplication to save time and money and reduce errors, but they also provide a single source of truth for your organization to give you data integrity.
ERPs are capable of connecting every department in your organization (finance, purchasing, engineering, operations) by connecting both the systems and the people who use them.
Simply put, an ERP is the best solution for integrating people, processes, and technologies across a business — the advantages of which are almost endless.
Why ERPs Are Critical To Your Manufacturing Business
An ERP system improves every aspect of your business, impacts every one of your departments, and makes your business more profitable.
Advantages of Using an ERP:
- Connect and integrate all departments within your organization
- Easily share data between divisions to streamline processes
- Reduce inventory costs
- Use consistent infrastructure from the shop floor to the front office, with all business activities having the same look and feel
- Increase throughput by automating processes
- Use accurate data and reports to track progress, productivity, and performance
- Deliver more jobs on time
- Eliminate purchasing errors
- Increase user-adoption rates through common user experience and design
- Reduce risk through improved data integrity and financial controls
- Lower operational costs
- Improve job costing
- Simplify accounting processes by integrating the department with the rest of your organization
ERPs touch on and improve every part of your manufacturing business. Your operation will run more smoothly, you will make more informed business decisions, and you will reduce overall operational costs.
In short, ERPs do it all.
Get your eBook Scared to implement a new ERP?
"*" indicates required fields