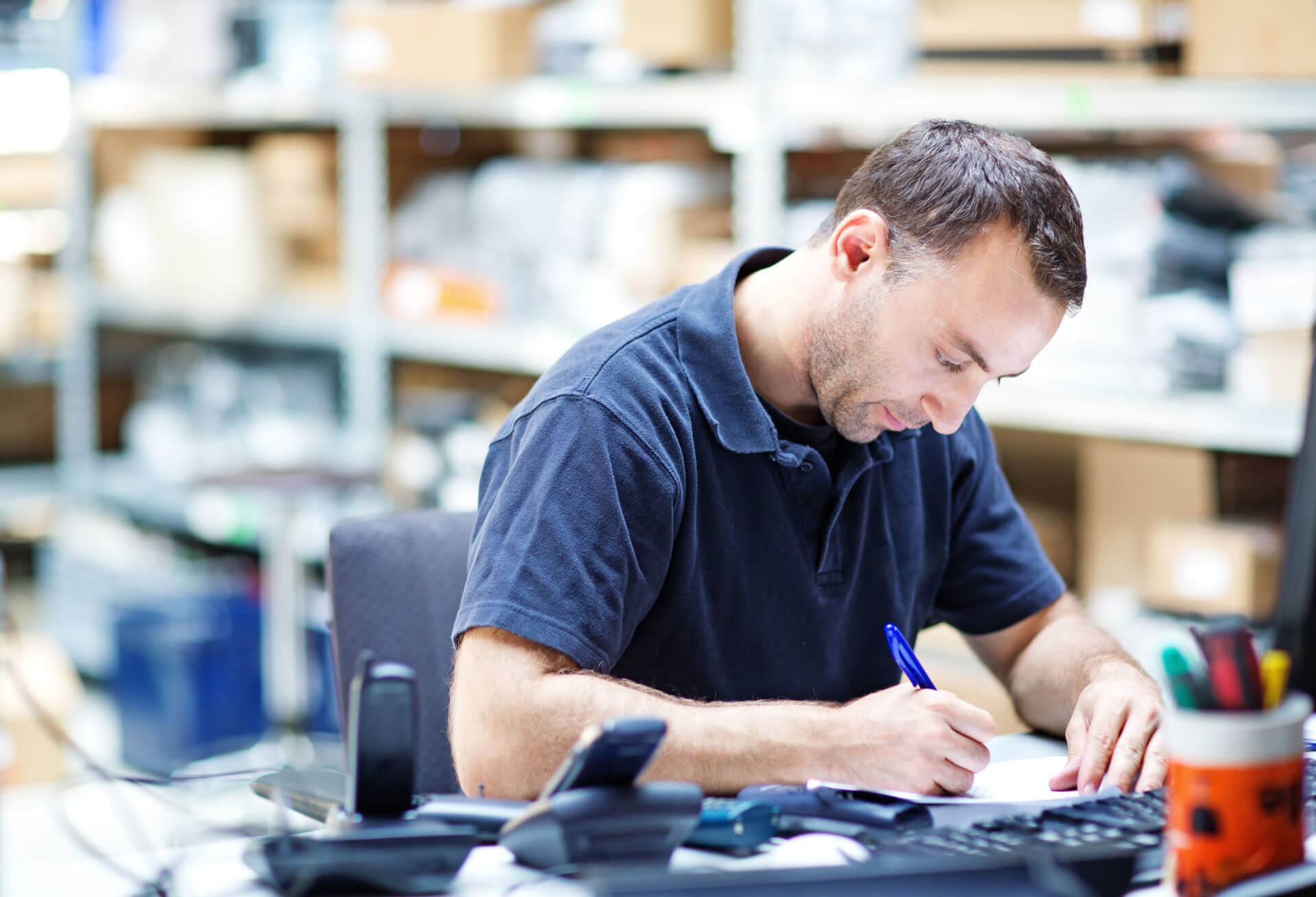
One of the most common questions we hear from manufacturers considering implementing an ERP for the first time is “how much is this going to hurt?” The simple answer is: some, but the more you prepare for it, the less it will hurt.
Implementing an ERP is disruptive — and it should be. It’s a system capable of improving every aspect of your business, it impacts every single one of your departments, and it can help make your business more profitable. If it was easy, it wouldn’t be very effective. Implementing an ERP is also one of the most time-consuming and expensive software projects a manufacturer will ever go through.
The fact that it’s going to be a challenge is not a bad thing, but you need to be honest with yourself about how much disruption you are prepared to take on before you get started. You and your whole team will have to be honest with each other and make a plan to succeed. Proper preparation will help you identify and overcome the challenges you’re certain to face.
Here are the 15 most common mistakes manufacturers make when they are selecting, implementing, or working with an ERP.
ERP Mistake #1: Poor planning.
We can’t emphasize enough how important planning is to a successful ERP implementation. Bringing an ERP on board will affect every department in your organization from engineering, to purchasing, to operations, so you will need to have a solid plan in place to tackle such a huge project. Many manufacturers do not do enough planning up-front, leading to confusion down the road, which either delays or derails the ERP project all together.
To solve this problem, manufacturers should plan, plan, and then plan some more! Think through how you are going to implement your new system, what your priorities are, and which departments you want to start with. Having a solid plan in place will give you a good roadmap to follow, and will help you get back on track when you inevitably hit a bump along the way.
In addition, manufacturers should put together an ERP evaluation team composed of stakeholders from departments across the company. This will help the implementation process go forward with fewer difficulties, as you’ll have someone to turn to in each department, to help put the new system into place.
We also suggest you conduct an internal audit of all your processes before choosing an ERP system, so you’ll not only know where you are currently at, but you’ll be able to more easily map your current tasks and processes into the new ERP.
ERP Mistake #2: Not having a project sponsor.
This is related to mistake #1, but you need to pick an employee to be the sponsor of your ERP system, someone who will act as a champion for the entire project internally. This employee can’t be just anyone either — it needs to be someone with excellent communication skills, as well as someone with considerable sway and influence within the company. This person will be responsible for the implementation of the entire system, and will be the point person every department can turn to, to help bring everyone within the company on board with the project, as well as a resource to consult when a complication occurs along the way.
ERP Mistake #3: Not evaluating your needs.
The only way you will find the right ERP system for you is to truly understand your company and what you need. Sit down with the team you have assembled and take some time to evaluate what you are doing well and where you need help. Think about where you have the most problems: maybe it’s tracking inventory, or maybe it’s scheduling your employees’ time on the shop floor. Once you know what you need help with, you can start looking for an ERP system with features that will address these shortcomings.
ERP Mistake #4: Not checking references.
Too often manufacturers are dazzled by a salesperson’s pitch, but then when it comes time to implement the ERP, they are surprised by the system’s lack of capabilities and functionalities. Many salespeople will also oversell the speed in which an ERP can be implemented. Don’t believe ERP providers who tell you their system can be put into place in a matter of weeks, as realistically it takes months to get an ERP smoothly up and running.
The best way to vet vendors? Ask for references. A good vendor will be able to provide you with at least three references of companies in your sector that have used their system. Call up these manufacturers and ask about features, functionality, and challenges — and don’t forget to ask how long it actually took to get the ERP up and running. You’ll get a better judge of vendors by talking to their customers than their salespeople alone.
To really dig into how you should manage an ERP selection process download and read our ebook. We studied hundreds of ERP competitions and talked to dozens of manufacturers to understand exactly what needs to be done to ensure you choose the best ERP for your business. We’ve streamlined the process, and created an easy to follow checklist that will guide you through the entire process, from creating your selection team, to vetting vendors, to making your final selection.
ERP Mistake #5: Underestimating the time and resources required.
All manufacturers grossly underestimate the time and resources required to implement a new ERP system. How can you calculate the actual time involved in implementing an ERP? A rough estimate to figure out how much time you’ll actually need is to divide the cost of the software by 100. For example, $50,000 for software will take approximately 500 man-hours or about three months to implement using a certified consultant. And expect to double that number if you plan to implement the system yourself with minimal professional assistance.
ERP Mistake #6: Not having key people on board from the beginning.
This also goes back to mistake #1, but you really need your key players from all departments on board from the beginning of the project. Too often manufacturers don’t put the right team together from the start, and the implementation process lags because key stakeholders and decision-makers aren’t involved with the process.
ERP implementation is one of the biggest and costliest projects an organization can undertake, and you need to get everyone on the same page right from the beginning. Far too often, manufacturers focus only on getting executive sign-off, instead of gathering key stakeholders from across the organization, after all these will be the people putting the system into place — not your executive team. If you involve the right people from the beginning you’ll have a key group of employees who are actively engaged with the ERP implementation process, and who have an investment in getting it right, right from the very start.
ERP Mistake #7: Not communicating vital information across departments.
We’ve said it before, but it bears repeating: not only is implementing an ERP disruptive, it will also affect every department in your shop — but once you get your ERP up and running it will streamline your entire business and make you more profitable. To make your implementation process move along smoothly, you have to make sure that all departments are sharing key information, and constantly in contact with each other. Before you start the implementation process, put a communication plan in place to keep things rolling, and make certain everyone knows what information they should be sharing, and who the contact points are.
ERP Mistake #8: Trying to do it all at once.
When implementing an ERP system, the single most important thing a company can do to minimize delays is to focus on one task at a time. It may seem counterintuitive, but you’ll go a lot slower if you haven’t set priorities, and are trying to do everything all at once. Start with the features and departments that are most important to you. Planning ahead of time makes you identify which features are the most valuable to you, and helps you understand that certain functionalities are dependent on others already being in place: you can’t accomplish D, until you’ve got A, B, and C up and running.
ERP Mistake #9: Not having a resolution process in place.
Implementing an ERP is a complicated task, so plan for problems to occur during the onboarding process. Too often manufacturers won’t have a plan in place for what to do when something goes wrong, and when that bump in the road inevitably occurs, they get stuck because they don’t have a resolution process in place. Create an issue resolution process before you start, to know who to turn to when you have a problem. This will help you resolve issues quickly and avoid costly delays.
ERP Mistake #10: Not investing in training and change management.
We can’t emphasize enough that implementing an ERP system, like all big changes, will be disruptive, and that they’ll be a few growing pains along the way. Not preparing your staff for the change, and not giving your staff enough training on the new system are some of the most common reasons that ERP projects fail — and they can also result in employees resenting the new system because they don’t understand the point of the system, or how to use it. To improve your chances of ERP success, make sure employees have a chance to become comfortable with the new system before it goes live. Communicating with your staff, and providing adequate training, will remarkably improve your implementation process.
ERP Mistake #11: Underestimating the importance of accurate data.
It may be a cliche, but it’s true: garbage in equals garbage out. It’s important to ensure you set up your ERP system with clean and accurate data, to minimize the likelihood of errors, and to ensure that you have proper procedures and parameters in place. ERP systems are amazing tools that can transform your business, but at the end of the day they can only work with the data you give them. Set the system up right from the beginning and you’ll have far fewer issues down the line.
ERP Mistake #12: Not doing proper testing.
The best way to see if your system is up to speed, and performing like you need it to, is to test it. But, you won’t be able to see true results based on a couple of test users. To see if your new ERP system is working effectively, you must simulate your entire user load in order to see the real-world effects of changes. Taking the time to do proper testing will, in the long run, make your implementation go faster, and will better set you up for success.
ERP Mistake #13: Not having a maintenance strategy.
Like all your tools, ERPs need proper maintenance to keep functioning at full capacity. Scheduling preventive maintenance will ensure you are taking full advantage of your ERP investment, and will limit the chance you’ll run into a big problem, which could end up costing you a lot of time and lost productivity down the road.
ERP Mistake #14: Not utilizing key features.
It’s surprising how many manufacturers don’t know or understand how to use key features of their ERP. When you don’t know how to effectively use all the functions and features, you’re missing opportunities to automate business processes, complete functions faster, and meet business objectives.
To overcome this hurdle, create a master list with all of your ERP’s features and functionalities, and track what features are actually being used by your employees. Periodically review the list to determine which features are being used consistently and which are the most helpful to increase your shop’s throughput. This will help you get the most out of your ERP.
ERP Mistake #15: Not retiring redundant software applications.
Your new ERP system is probably taking the place of one or more of your current software applications. Make sure your staff stops using these old and redundant systems, and uses the ERP to its fullest capacity. Keeping these old systems in place will not only cost you money as you’ll continue to pay for licensing, maintenance, and upgrades to these old systems, but will also undermine the effectiveness of your new ERP. Your new ERP will connect multiple departments, and streamline your organization, so make sure all staff member are using the system properly. This goes back to mistake #10 — if you give your staff adequate time to adapt to the new ERP, they will be less likely to stick with old applications.
A good ERP will help manufacturers streamline workflows, improve throughput, and cut costs. Avoiding the mistakes we outlined above will help you implement your new ERP system quicker and easier, letting you avoid lost productivity and costly delays, and helping you get the most out of your new ERP.
Get your eBook Scared to implement a new ERP?
"*" indicates required fields