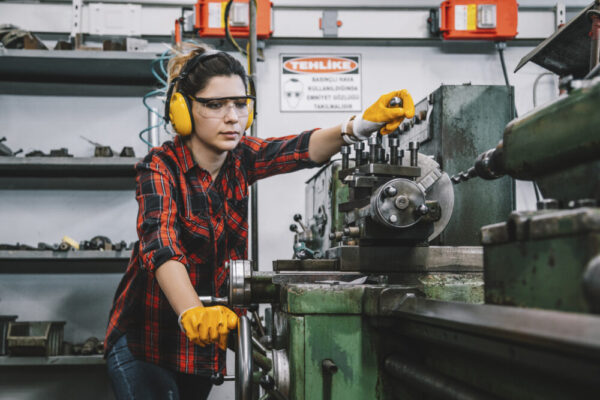
DBR, or Drum-Buffer-Rope, scheduling sounds elaborate and complicated. But, it is actually a simpler and smarter way to schedule your custom manufacturing shop—and one that you should think about embracing. Curious? Keep reading below:
Welcome to the second installment of our series on DBR scheduling! Last week we walked you through what exactly is DBR scheduling, click here for a refresher, and talked about how DBR scheduling can simplify your scheduling and let you create better and more accurate shop floor schedules. This week we will dive a little bit more into the benefits and advantages of DBR scheduling.
Recap—What is DBR scheduling?
In a nutshell DBR scheduling is a scheduling tool that does away with complicated algorithms that need spools of complex and hyper-accurate data—data that your custom shop doesn;t have and isn’t able to produce—and instead takes a more common-sense approach to scheduling your shop.
A DBR scheduling tool identifies the resource or work center in your shop that is slowing your operation down, a Drum, or bottleneck so-to-speak, and uses that as the basis for managing and creating a schedule for your shop. A DBR tool creates a schedule, and a series of priority management systems (Buffers and Ropes) that ensure the bottleneck is always working at full capacity—which means that your shop is always working at full capacity—translating into more jobs completed and out the door on time.
Advantages of DBR scheduling
DBR scheduling will deliver a number of returns to your shop, but the biggest advantages that it can offer are:
- Decreased lead time
- Increased throughput
- Better communication and priority management
Decreased lead time
As a growing custom manufacturer, keeping on top of lead time is one of the most difficult tasks that you face—and you have probably lost orders to competitors over this. Your competitors don’t build a superior product to yours, but they are able to quote and then deliver jobs on time.
Your customers want to know the delivery date for the product they have ordered from you, and your sales team is often nagging you for this information, wanting to provide an ETA to the customer during the sales process. But if you are using a traditional manufacturing scheduling system, estimating delivery times is an educated guess at best.
DBR scheduling lets you manage your plant better, and instead of constantly being lost in the weeds, a DBR schedule keeps you running at maximum efficiency, which means you can give your customers more accurate estimated delivery dates—and then, more importantly, follow through and deliver their job on time.
Instead of jobs getting stuck at bottlenecks on the production floor, causing you to live in a world of constant chaos and delays, DBR scheduling prioritizes these problem areas in your shop. Jobs will no longer pile up at these work centers as your shop is precisely scheduled to ensure work is always flowing through these centers at a pace that they can handle—essentially preventing bottlenecks before they occur.
In fact, you can think of a DBR Buffer as a bottleneck buffer, designed to ensure that all prerequisite activities are completed before the Drum, that pesky work center that was always causing you trouble, is scheduled to begin work. And because of how a DBR schedule is configured, buffers don’t add time you don’t have to a job—they actually ensure everything runs smoothly and on time. Meaning you can decrease the amount of time it takes you to finish a job.
Increased Throughput
This is perhaps the biggest benefit of DBR scheduling, as you are able to schedule your shop to its actual maximum capacity, and increase your throughput levels. Instead of building a schedule based off of guesswork, a DBR schedule is developed around, and built to support, the resource in your shop that slows you down. A DBR schedule lets your shop run at its most efficient level and maximizes throughput.
And just a quick reminder, throughput is the most crucial measurement for your shop—but many manufacturers get throughput wrong: The correct definition of throughput isn’t the amount of time it takes to complete a finished good, but the rate at which the system generates money through sales. It’s important to remember that throughput is linked to sales, as making money is the goal after all.
Remembering to define throughput in terms of sales will ensure that you are scheduling your shop correctly. It’s no use pushing jobs through your shop, and parts through your bottlenecks if they are only going to sit on your shelf as inventory. You need to ensure that the jobs you are prioritizing, and the jobs that you are moving through your bottlenecks, are the jobs that you have customers waiting on. DBR scheduling is designed to, and will maximize the throughput of your shop—just ensure that you are setting the right priorities to maximize profits.
Better communication and priority management
You need to ensure that your staff are working on the right set of priorities to ensure jobs get completed and out the door on time. Instead of always scrambling to get jobs done, and sorting out miscommunications with your staff, a DBR scheduling tool creates a detailed schedule in which each job and task on a project is prioritized and scheduled in turn.
With a DBR scheduling tool, every department and role in your shop will be better equipped, and miscommunications will become a distant memory. Managers and supervisors will be better able to set and manage priorities as well as define and follow the throughput of your shop. Production managers will always know what needs to be done and when, and will ensure that everyone in your shop is working on the task they need to be doing, to get jobs completed.
Your staff will be able to move smoothly from one job to the next, and will never have to question what job or task they should be prioritizing. DBR schedules give you peace of mind that jobs will pass as planned through your shop, and out the door on time.
Get your eBook Scared to implement a new ERP?
"*" indicates required fields