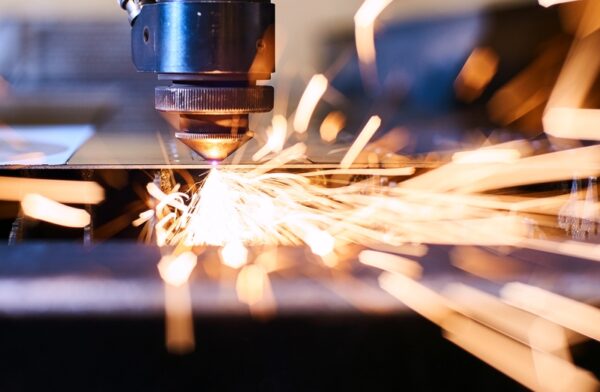
An ERP (Enterprise Resource Planning) system is a suite of integrated software applications that manage core business processes. ERPs give manufacturers visibility over their entire operation, allowing them to increase efficiency, improve productivity, and lower costs.
In today’s marketplace, many different types of ERP systems are available. While this increases consumer choice, it can make it difficult to understand and know which kind of system is best for your business. Below we will unpack the differences between two types of ERP systems — generic and industry-specific — to help you figure out which system is right for your manufacturing business.
Types of ERPs
Generic ERP Systems
Many of the biggest, well-known ERP systems are generic or generalist ERPs. Generic ERPs are very robust systems that offer a wide range of features and functionalities. Generic ERP systems can adapt to processes used by companies across various industries, but require customizations and add-ons to do so.
Industry-Specific ERP Systems
Industry-specific ERP systems are designed to meet the needs of a certain industry. They are often developed by smaller, niche companies that are made up of a team of industry experts with the sole focus of solving the special needs of their industry. Industry-specific ERP systems include the same features as generic systems — accounting, finance, inventory management, project management, etc. — but will also have features that target the unique needs of the industry for which they were built.
For example, an ERP system designed for the manufacturing industry will include an MRP (Materials Requirement Planning) module, along with other customized features that manufacturers need. Industry-specific ERP systems are out-of-the-box ready as they do not require customizations to create industry-specific features and capabilities.
Cons of Generic ERPs
Generic ERPs are a one-size-fits-all solution. They are often designed and created by some of the biggest names in the business (think Oracle or Microsoft). While they are robust systems full of many great features, they require a high degree of customization. This in itself isn’t a bad thing — but it is expensive.
For starters, implementing a generic ERP system is more timely and costly than implementing an industry-specific ERP because it takes time to build the needed customizations.
RELATED ARTICLE: Why a long ERP implementation timeline can derail your project
Customizations are also more expensive — not only because the implementation phase is longer and therefore more costly — but you also must pay for the customizations and add-ons you need. Long-term system maintenance is more expensive too, as customizations will require time and attention from your ERP provider for upkeep.
You can dramatically reduce these costs by using an industry-specific ERP system. Distinct features and integrations will already be pre-built into the software, meaning no need for enhancements and it is faster to get the system up and running in your shop. Not only does this shorten the time and cost of implementation, but it also gets you reaping the benefits of an ERP quicker — something both you, and your finance department, will like.
Pros of Industry-specific ERPs
Industry-specific ERP solutions are built to offer comprehensive functionality for a specialized market segment. They have greater, more tailored capabilities because they have been designed with a deep understanding of industry-specific processes in mind. In addition to the shorter implementation timeline, reduced implementation costs, and lower system maintenance fees, industry-specific ERPs can offer a higher level of functionality — at a lower price point. These systems offer standard features and capabilities that are tailored to your industry and operational needs, that generic ERP systems simply can’t provide.
Along with the basics like accounting, business intelligence, and inventory management, custom manufacturing-specific ERPs will include features specific to custom manufacturers like product engineering, quoting and estimating, job costing, shop-floor scheduling.
Because these systems are designed with a particular industry in mind – and encompass that industry’s unique processes – there is often a better understanding of what the end-user of the system needs. Not only does this make for a more functional solution, but it also makes for easier and more efficient communication between ERP provider and manufacturer The ERP provider will speak your language, and should have a higher level of understanding of your unique needs.
Some Final Thoughts
Both generic and industry-specific ERP systems can provide manufacturers with the features and functionalities they need to improve their operations. But generic ERP systems will require a high level of costly customizations, whereas industry-specific ERPs are already tailored to the needs of manufacturers. Manufacturers can get a system with greater capabilities, quicker and cheaper, with an industry-specific ERP.
Get your eBook Scared to implement a new ERP?
"*" indicates required fields