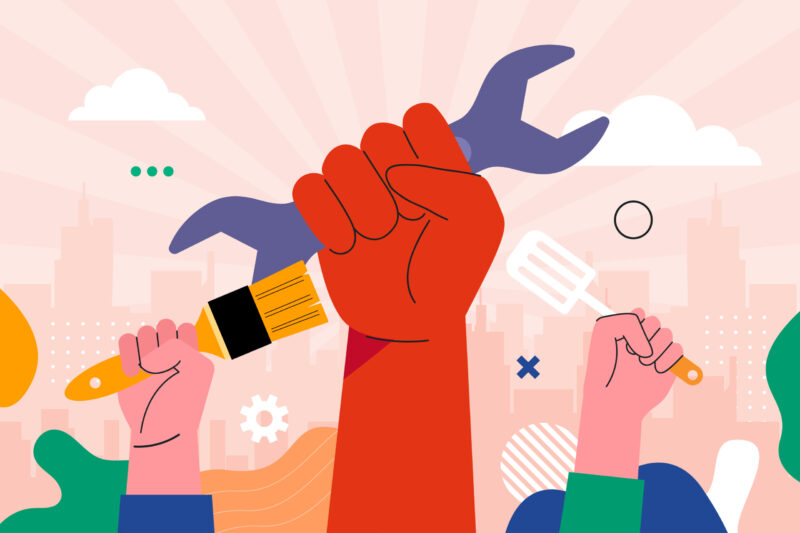
Labor issues continue to vex manufacturers, with labor shortages remaining one of the biggest struggles within the industry.
Though the number of job openings has fallen over the past year, there were still 582,000 unfilled positions in the manufacturing industry in June 2023, according to the U.S. Bureau of Labor Statistics. Compared to June of 2022, which saw 852,000 job openings in the United States, the labor shortage is easing—but with an aging workforce and reshoring continuing to be a trend that is bringing more jobs back to North America, labor shortages will continue to be an ongoing issue within the industry.
What jobs are manufacturers having trouble hiring for?
1. Production Workers
Many of the jobs that manufacturers are struggling to fill are on the shop floor. Manufacturers continue to face stiff competition from other sectors, including warehousing and retail—think Amazon—offering high wages to attract job seekers. Also, as the manufacturing world becomes increasingly complex and connected, manufacturers are looking for entry-level workers who can understand and operate new technologies, which takes many blue-collar job seekers off the table, making it difficult for manufacturers to find and hire qualified shop floor workers.
2. Engineers
Some manufacturers are also struggling with hiring engineers. With fewer students pursuing engineering degrees, and an aging workforce nearing retirement age, there are not enough qualified engineers on the job market. The U.S. has long seen a trend of fewer domestic students enrolling in engineering programs, but for many years international students were making up the difference. However, policy changes that limited international student enrollment, along with pandemic restrictions, mean there are now not enough engineering graduates to fill current needs.
3. Tradespeople
Declining enrollment in trade programs over the past decade is also starting to show. With more young people pursuing undergraduate degrees, there is a void of qualified tradespeople. Particularly lacking are electrical, mechanical and automation technicians, as well as CNC machinists, welders and maintenance mechanics. Coupled with this general lack of tradespeople is the need for skilled technicians who can work with new and emerging technologies, even further shrinking the pool of qualified candidates.
What can manufacturers do about the labor shortage?
1. Promote STEM Careers in Manufacturing
Getting more young people and students interested in not just STEM careers, but STEM careers in manufacturing is an important step the industry can take to attract new talent. For too long, the manufacturing industry has been overlooked, even though it offers interesting—yet well-paying and stable—jobs, and is a field where young people can build careers where they have the opportunity to interact and use the latest technology. Manufacturers need to promote their industry more and show it is a great place to work.
Curious how you can promote all of the exciting things your shop has to offer? Think about hosting a Manufacturing Day event.
2. Leverage Technology
Everything from ERPs to automation can help manufacturers alleviate the labor shortage and become more efficient with fewer workers. For example, ERPs facilitate seamless coordination across various departments, enabling real-time data sharing and informed decision-making, and automation enables machines to perform tasks that would otherwise require significant human involvement, reducing the need for a large workforce.
Technologies like these not only help manufacturers maintain output levels but also allow them to allocate their human resources more strategically. However, as you embrace technological innovation, it is essential that your current workers are not left behind. Investing in training and upskilling initiatives is imperative and will empower your employees with the skills necessary to navigate new technologies and ensure your shop runs as efficiently as possible.
3. Focus on Retention
Some within the manufacturing industry think that the problem is not, in fact, with finding and recruiting new workers, but with retention. Is your workplace lacking in diversity? This could mean you are losing out on a valuable source of talent.
The manufacturing industry needs to create a more inclusive culture that makes women and other non-traditional STEM workers feel included. For example, women and other employees from non-traditional backgrounds often feel like they must constantly keep proving themselves by taking on more work, which leads to higher rates of burnout and turnover. Overcoming systemic issues related to gender and race, and creating a culture of inclusivity where everyone feels valued can help you retain—and attract—talent to your workplace.
4.. Look Outside the Usual Talent Pools
To find great workers, focus on hiring trainable and teachable people. Maybe not everyone who applies for a position at your company will have the necessary skills you want them to have, especially those related to technology. But, if you focus on hiring people with a strong work ethic and the ability to learn and grow, you can turn them into the skilled workers you seek. Expand your candidate pool and look outside the usual places: For example, have you ever looked into things like ex-offender staffing schemes to find interesting, talented and teachable people you might be overlooking?
You must also invest and focus on training new hires to help support them. Give your staff—both new hires and those who have been with you for years—the tools they need to understand new technologies and thrive in your shop. Well-trained workers will add value to your workplace and help your company succeed.
Happy Labor Day! We know that the labor shortage issue will not correct itself overnight, but hopefully, we have given you a little food for thought, as well as some ideas on how you can attract and retain new talent to both your shop and the manufacturing industry as a whole.
Looking for more ways to improve your shop? Download our guide to Becoming a Manufacturing Superhero to gain insider tips on improving your company’s performance and creating a better workplace.
Get your eBook Scared to implement a new ERP?
"*" indicates required fields