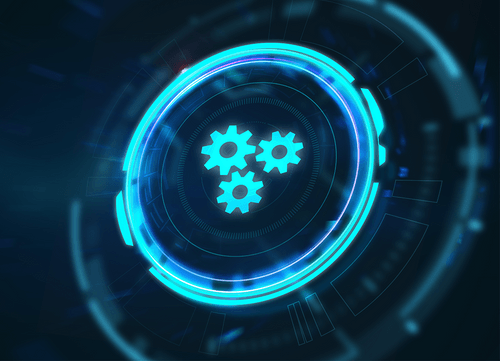
As manufacturers seek ways to improve efficiency and lower expenses, automation, Industry 4.0 and other connected manufacturing solutions are gaining in popularity. Automation especially — while not a new concept — is seeing advancements in technology that are making it more widespread and easier to implement.
How much automation is right for you depends on the size of your operation and budget, the type of manufacturing you do and the specific goals and priorities of your business. Read on to learn the advantages and disadvantages of automation, as well as some things to consider when deciding to implement automation in your shop.
What is Automation in Manufacturing?
The goal of automation is to improve efficiency, productivity and accuracy in manufacturing processes by reducing manual labor and eliminating the chance of human error.
Manufacturing automation involves using equipment to automate systems or processes to increase production capacity and decrease costs. It can be especially useful for repetitive tasks, dangerous tasks or tasks requiring extreme precision. Automated inventory management, scheduling, and data analysis for reporting are other ways in which automation can help improve manufacturing processes.
It’s important to note that automation will not replace the need for human workers in the manufacturing industry. Humans are still necessary for most manufacturing operations and processes, and instead of replacing roles, automation will lead to a change in roles. With automation, workers can be better utilized in safer, less physically demanding roles focusing on problem-solving, creativity, people management and innovation. Automation can improve productivity and job satisfaction for employees while also enhancing overall workplace safety.
What Are the Benefits of Automation?
1. Reduction in Production Time
Automated machinery can manufacture products with fewer defects in less time. Using machines, robots or automated processes for specific tasks means that these tasks can be accomplished with greater speed and precision than by human workers. As a result, manufacturing and production time is reduced while also allowing workers to complete more complex tasks.
2. Increased Accuracy and Repeatability
Automated machines that are programmed to perform repetitive tasks exhibit a greater degree of accuracy and repeatability compared to humans.
3. Improved Product Quality
By using advanced sensors and robotics, automated machinery can complete inspection processes to boost quality control. Automation also facilitates the collection of real-time data about products, which enables manufacturers to refine quality control checklists, detect substandard components and replace them with high-quality ones.
4. Faster Response Times
Real-time data empowers manufacturers to make informed decisions about stock levels and improve delivery rates by letting you know if you can start production right away or if you need to order more materials before you can begin a job.
5. Reduced Human Error and Danger
Automation reduces human error, which not only improves the quality of products and lowers the risk of recalls and repair expenses, but reduced levels of human error also enhances safety and lowers the risk of injuries.
6. Assistance with Labor Shortage
Automating mundane and repeatable tasks can mean fewer workers are needed in a shop, mitigating the impact of the labor shortage that manufacturers are currently facing.
7. Improved Analytics and Production Tracking
Automation technology uses sensors, robotics and advanced equipment to track inventory, system maintenance and finished products. This enables more optimized planning and scheduling, streamlined operational processes, better decision-making and improved ROI.
What Are the Disadvantages of Automation?
1. Large Initial Investment
Automated machines can be a costly investment for companies, especially small manufacturing businesses, with prices ranging from thousands to millions of dollars, depending on the level of automation required.
2. Unpredictable Costs
There may be unpredictable costs associated with automation, such as research and development costs, preventative maintenance costs and the cost of training employees to operate automated technologies — which in some cases may exceed the actual cost savings from automation.
3. Less Versatility
Using machines for specific tasks can reduce the adaptability and variety of functions that an employee does. This can lead to an increase in employee turnover, which can ultimately impact the company’s productivity and profitability.
How Much Automation Is Right for You?
Automation has been around for decades in manufacturing, but with recent advancements in AI, robotics, machine learning, IoT and other digital manufacturing technologies, automation is becoming more advanced, more prevalent and more accessible.
While automation can be a competitive advantage for many manufacturers, the decision to implement it in your shop should consider your specific operations and your production quantities. Smaller manufacturers with low production runs may benefit from automated machines less than larger facilities with medium to large production runs.
Manufacturers must carefully evaluate their unique needs and goals, as well as their budget, before making a decision about implementing automation in their manufacturing operations. Ensure you do a cost-benefit analysis of automated technologies before implementing them in your shop, being sure to include the long-term return on investment, as well as maintenance costs and potential technological obsolescence.
Small manufacturers should remember that they can benefit from automation in many ways beyond automated machinery and production lines. For instance, digital technologies can help automate inventory management, orders, purchasing, and even marketing processes. One tool that can help small manufacturers automate these processes is an ERP (Enterprise Resource Planning) system, which can integrate and manage all aspects of a company’s operations, including supply chain, financials and customer relationship management from one system.
ERPs streamline and integrate various functions such as inventory management, production scheduling and order processing into a centralized system, enabling efficient and real-time data sharing across departments and facilitating smoother operations. This automation eliminates manual tasks, reduces errors and enhances overall productivity, allowing you to optimize your resources, reduce costs and improve operational efficiency.
Interested in learning more about how ERPs can help you automate key business processes? Check out reason number 2 in The Top 5 Reasons You Need an ERP.
Get your eBook Scared to implement a new ERP?
"*" indicates required fields