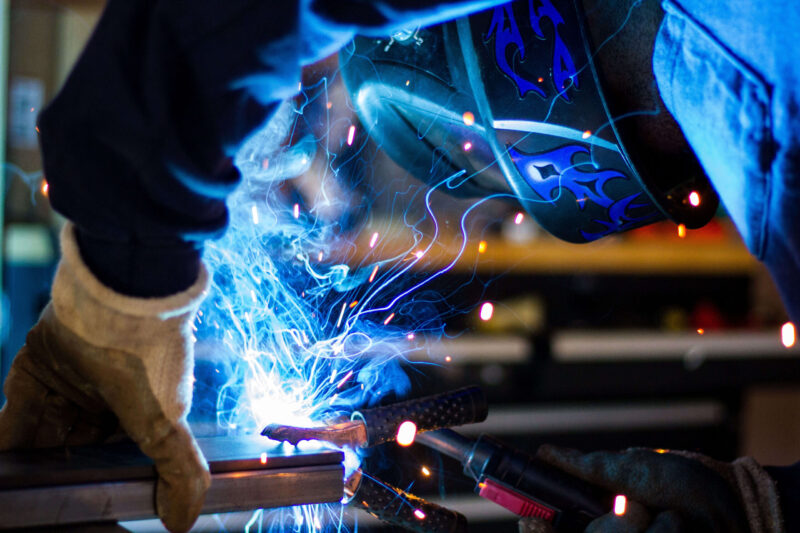
Engineering is a key component of ETO manufacturing environments — it’s part of the name for goodness sake! — but engineering is all too often left out of ERP software systems.
Engineers need an ERP system that meets their unique needs, including creating and managing Bills of Materials (BOMs), automating routing steps, and connecting CAD systems — but they also need a system that integrates the engineering department into the rest of the shop to increase efficiency and improve business processes across the organization.
What Do Manufacturers Need From Their ERP?
The manufacturing industry is unique, and manufacturers need an ERP that has features and functionalities designed specifically to meet their needs. Common features that manufacturers need in an ERP system include inventory management, accounting, scheduling, production planning, along with quoting and estimating.
Manufacturing is also one of the most data-heavy industries out there today. ERPs can help you harness the power of your data — through collection and analysis — to better understand your shop’s performance which, in turn, will help you increase efficiency and give you a competitive advantage over your competition.
What Do ETO Manufacturers Need From Their ERP System?
ETO (or engineer-to-order) manufacturers, however, are unique in that they are always designing, engineering, creating, and building unique and custom products, meaning they never really build the same thing twice.
This poses some unique challenges for ETOm manufacturers and it’s essential to find an ERP with the right built-in modules that can help you meet these challenges, and make your shop run smoothly and efficiently.
But many ERPs, even those that are designed for the manufacturing industry, all too often leave the engineering department out of the loop. Most manufacturing ERPs will connect many departments and functions in a shop — accounting, purchasing, scheduling, inventory management, to name a few — to improve manufacturing processes, but the engineering department, which plays a key role in the designing, engineering, and manufacturing of a product, is left out of the loop.
What this means is that engineers are tasked with hunting down and re-entering information from and into spreadsheets, CAD software, and other systems. This not only wastes valuable time and increases the chance for human error, but it also decreases the productivity and efficiency of the engineering department.
What Do Engineers Need Out of Their ERP System?
One of the most cumbersome and detailed tasks of the engineering department is to create a bill of materials(BOM). Many manufacturing ERPs will require the engineering department (or possibly purchasing or someone else within the company) to painstakingly take a CAD drawing and create a list of all the parts needed, and then create the BOM. To get this information synced up with the rest of the ERP, it must also be re-keyed into the ERP system.
The best manufacturing ERP systems will do this for you — and will connect your CAD software to your ERP. This saves you all of the above steps and lets your ERP interact directly with your CAD software.
Imagine being able to produce a BOM from a CAD drawing at the touch of a button!
ERP systems that are built to work with CAD software can automatically extract and create a BOM from the designs and drawings that your engineering department creates in CAD — which not only saves your engineers time, but additionally streamlines purchasing, requisitioning, and manufacturing processes.
Your engineers or draftsmen will no longer need to waste hours manually creating BOMs. You can be assured that fewer errors will be made and that your BOMs will be connected to vital systems like inventory management — meaning it’s easier for you to know what parts are needed and what parts need to be ordered to get a job built and out the door.
New Challenge: Increased Customization
You may also be noticing that your engineering department’s job has been changing recently.
In the past, your draftsmen provided your shop with drawings based on specs from your customers, but now you may be finding that many of your customers are designing their own products.
This trend has forced you as a manufacturer to gain more knowledge about designing, assembling, and manufacturing parts in a more efficient and cost-effective environment, and to learn how to comply with Design for Manufacturing (DFM) principles.
What this translates to, is that today you probably have more people working in the engineering room than ever before — and that you have to go beyond the basic design processes you used in the past.
After identifying what will be purchased or manufactured you must now define the routing steps. To make this process easier, many manufacturers are managing the routing steps and the instructions straight from the 3-D CAD Software to speed up the process once the design is completed and to decrease the potential for mistakes on the production floor. Having an ERP that can seamlessly connect to your CAD system will help manage this process and will allow you to automate routing steps.
Closing Thoughts
Engineering is one of the most important elements in the custom manufacturing environment. Finding an ERP that gives engineers with they need will improve your manufacturing processes and let you get jobs out the door faster and better.
Looking for an ERP that includes engineering? Check outGenius ERP.
Get your eBook Scared to implement a new ERP?
"*" indicates required fields