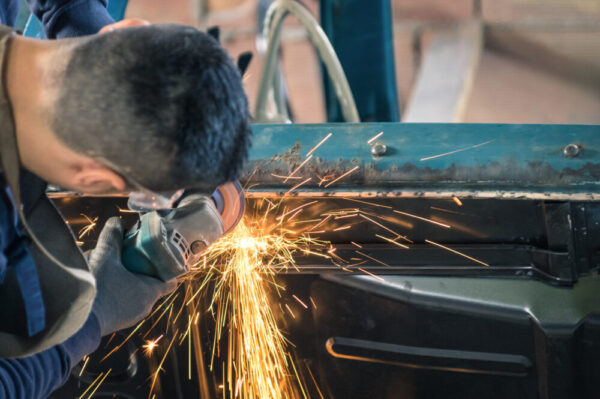
Selecting the right ERP for your business is a very personal choice — after all, every manufacturer is unique and has different needs and requirements.
ERPs are all about fit and the right one for you will vary depending on your business, your industry, your size, your budget, and your needs. What may be the best solution for the custom manufacturer down the road may not be the best solution for you. To find the best ERP for you, you need to take a hard look at your business, your strengths, your weaknesses, and your needs before you can find the one best suited to you. (If you are struggling with this process, check out our blog on what is the best ERP or download our ERP selection ERP — both will give you good ideas and steps to take to find what fits your business best).
That being said, there are a few modules and features that custom manufacturers should be on the lookout for when picking the ERP best suited to them. Custom manufacturers are unique in that they are always engineering, creating, and building unique and custom products, meaning they never really build the same thing twice. This poses some interesting challenges for custom manufacturers, and it’s essential to find an ERP with the right built-in modules that can help you meet these challenges, and make your shop run smoothly and efficiently.
Below are the top 4 modules we think every custom manufacturer needs:
Inventory Management Module
Inventory management, including the managing of long-lead items, is a major issue for custom manufacturers. To have a job flow through a shop effectively requires having the right materials on hand at the right time. Keeping track of inventory, and knowing when you need to order critical parts or raw materials is something that custom manufacturers need to be able to do very effectively.
An ERP equipped with a robust inventory management system will integrate your inventory management with the rest of your operation, making tracking inventory throughout your organization easy. You will be able to keep track of the inventory you use on each job, which, for example, will let you do proper production planning as you will know exactly the amount of raw materials you have on-hand, and what you need to order to complete a job.
Knowing real-time stock levels also make it easier to replenish inventory — a good ERP can either automatically reorder materials for you, or send your purchasing manager a timely reminder letting her know that items need to be reordered.
You will be able to easily manage long lead-items, as you can know about these items during the design-phase of a project, and have more time to order the item and ensure you have it on hand when you need it. (To learn more about ERPs and inventory management check out our blog here).
Quoting and Estimating Module
Custom manufacturers often struggle with accurately estimating materials, labour and other costs and inputs to create a quote that is fair — but will still lets the business turn a profit, because it is difficult to create a quote for a truly custom product that hasn’t built before. ERPs can help custom manufacturing companies create better quotes, and better understand job costs. Instead of quotes and estimates being educated guesses at best, ERPs supply you with data that makes this process easier.
Although each product you build is unique, an ERP contains a stockpile of historical data from past jobs and products that you can access and analyze to help create better quotes.
The use of a robust and integrated ERP solution will also stop the guesswork that goes into job costing, by letting you use accurate and real-time data and metrics to determine real job costs. A good ERP tracks all of the costs of a manufactured item or a process including material, labor, equipment, outsourced operations, as well as other resources that are directly required to manufacture an item—helping you keep on top of profit margins.
Scheduling Module
Scheduling is another area that can be a major challenge for custom manufacturers. Balancing machine and labor schedules to ensure maximum efficiency is a difficult task for custom manufacturers, and one that requires a lot of insight into your operations, and the jobs you have on the go. Without an integrated system that connects and gives you data from across your organization the task is nearly impossible.
One of the greatest benefits of ERPs is their ability to provide comprehensive visibility. An ERP gives you an overarching view of your operations, letting you know how every aspect of your operation is performing, including your shop floor. An ERP can give you production statistics, like staff productivity and machining time.
And with an ERP what used to take hours of meticulous data collection, and report creation, can be done automatically giving you a comprehensive overview of your operation. You can use this information to optimize production schedules, for both equipment and labor—to maximize capacity and increase your throughput.
Finding an ERP with a Drum-Buffer-Rope scheduling system can really improve how you schedule your shop. Any custom manufacturer worth their weight in salt will tell you that trying to schedule a shop based on the hundreds of variables that go into a custom product — a product that has never been built and therefore doesn’t have any reliable data — will inevitably fail. And trying to incorporate changes into such a system is impossible and causes manufacturers to have to start from scratch, meaning wasted time, and decreased efficiency.
DBR scheduling, by giving you a better system for priority management, allows you to manage your plant better, and keeps you running at maximum efficiency. By using DBR scheduling, and revolutionizing the way your shop manages priorities, you will simplify the way you schedule your shop, and will be able to be more agile, and better equipped to deal with shifting priorities and to incorporate changes into your shop floor schedule. Learn more about how DBR scheduling will revolutionize your shop here.
Product Engineering Module
Do you know that up to 20% of the total engineering time in your shop is taken up by transferring Bills of Materials (BOMs) out of your CAD system? This is an especially time-consuming task for custom shops where every item you manufacture is truly unique.
But you can get this time back, and have your engineering department working on more important tasks than data entry, by having your ERP system integrate directly with your CAD software.
With a fully integrated system, your engineer will be able to seamlessly export the BOM from your CAD system into your ERP, creating a fully itemized list of the materials, and letting you easily compare the materials needed for the project against what you already have on hand. Not only will you save time and remove errors that come from manual data transcription and entry, you will always be confident about what materials you need to get a job done on time and on budget. Selecting an ERP with this functionality is key for custom manufacturers.
In a good custom manufacturing ERP system, this task will be fully automated and let you transfer data between a CAD system and your ERP with a push of a button, eliminating all redundant data entry, as well as being able to automatically reconcile, and find and correct any errors—if an edit is made to the data in the CAD system, you need this to update in the ERP system automatically. A system that automatically resolves discrepancies, but also lets the end-user have the final say, is the gold standard of CAD-ERP integration.
A fully integrated product engineering module will also alleviate design bottlenecks and will allow your engineering department to engineer from scratch, or use historical data, to design custom products and let you anticipate resource requirements with greater accuracy.
Conclusion
As a custom manufacturer you are a unique business — in more ways than one. Finding the right ERP for you, one that is equipped with the above four modules will help you become a more efficient and cost-effective business. You will be able to effectively oversee your manufacturing process, run your shop more smoothly, meet growing demands, and deliver unique and customized products to your customers.
Get your eBook Scared to implement a new ERP?
"*" indicates required fields