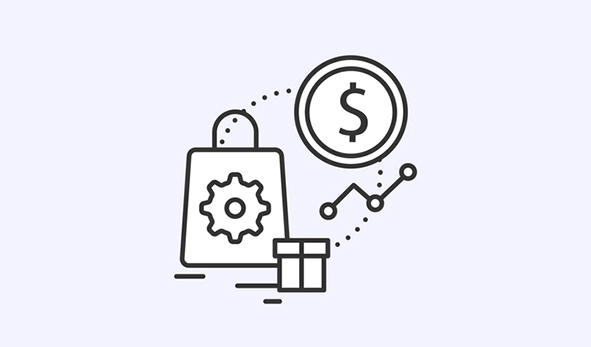
Why Do Purchasers Need an ERP?
An ERP makes purchasing easier for manufacturers by automating everyday purchasing tasks and providing accurate real-time data to ensure that you always have the right amount of stock on hand.
Purchasing, especially in custom or ETO (engineer-to-order) manufacturing environments, is a complicated task. Unlike in more standardized manufacturing environments, raw materials and parts aren’t required in a consistent or straightforward manner in custom shops. Coupled with the need to procure items with long lead-times — that often need to be ordered before the product has been fully designed and engineered — purchasing in ETO environments is stressful.
Too often, the purchasing department is blamed for delays and issues that are not their fault in the making — leading to unnecessary contention and conflict in your shop.
An ERP can alleviate the problem by streamlining the purchasing process through automating purchasing processes, providing accurate checklists of items to be procured, automatically monitoring inventory levels, and managing vendor relationships.
ERP Benefits for Purchasers
Streamlined purchasing processes
Think about the time and effort that go into purchasing: creating tracking numbers, filing orders, checking inventory, making a purchase history, coordinating with suppliers, and so on.
ERPs make purchasing easier by automating these tasks and providing you with accurate real-time data. An ERP is always managing your inventory levels in the background of everything you do, so you will always know what stock you have on hand and what needs to be ordered to complete a job. Most ERPs also let you create a PO with one click — saving you time.
ERPs keep track of which parts are required for which jobs, keeping you organized. A good manufacturing ERP — like Genius ERP — also includes an automatic reorder function. This feature alerts you when stock is running low and tells you it’s time to place an order — or even better, you can set it to place an order for you automatically.
Optimized supplier relationships
Managing relationships with suppliers is one of the biggest tasks a purchasing department is required to do. Using an ERP can help you create better relationships and streamline communications with vendors.
With an ERP, you can create a robust supplier database — essential to all manufacturers that order multiple parts from multiple suppliers. From names and addresses to parts and materials offered and tax identification data, your ERP collects and organizes all this supplier information into one database. You will always be confident that you have the correct information about your suppliers, making it easier to submit requests and orders.
Using an ERP to handle your supplier communications will also streamline the process: By using a purchasing portal that is fully integrated with your current jobs and existing inventory, you can make simultaneous pricing inquiries for multiple items to multiple suppliers — and receive prices from suppliers without having to re-enter any information.
An ERP will also increase the negotiating power of your purchasing department by aggregating POs to give you more power to negotiate with vendors and ultimately save money.
Improved supply chain management
ERPs streamline and automate purchasing tasks, not only helping you to increase productivity — but also improve your overall supply chain management.
Supply chain management has been a thorn in the side of many, if not all, manufacturers during the COVID-19 pandemic. Interruptions and delays have become the new normal, making procuring goods very difficult at this time. ERPs act as a “one-stop-shop” and provide manufacturers with a holistic, consolidated view of their entire supply chain, allowing manufacturers to make better-informed purchasing and procurement decisions.
ERPs help manufacturers improve their supply chain management in many ways, including:
- Integration of internal business processes;
- Enhancement of information flow among different departments inside the company;
- Better inventory management;
- Improvement of the company’s relationships and collaboration with outsourcing suppliers, customers, and supply chain partners;
- Streamlining purchasing processes;
- Increasing a manufacturer’s ability to evaluate vendors;
- And efficiently manage complex supply chain networks.
ERP Modules for Purchasers
Genius Vendors
Avoid interruptions and manage your supplier relationships with Genius Vendors. Our purchasing portal syncs with your projects and inventory, allowing you to control all of your vendor transactions in one place, ensuring that you always have the right materials on hand.
Genius Vendors lets you manage all your interactions with vendors in a single system — including quote requests, purchase orders, receiving, and invoicing — to better control costs. Easily create and send RFQs to multiple vendors, giving you the ability to evaluate vendors on several factors like on-time delivery, quality, and price, guaranteeing that you always choose the right supplier for every job.
Genius Vendors also includes a recommended repurchasing function that will identify potential shortages based on real-time inventory, expected delivery times, and in-process production orders.
Genius Inventory Management
Avoid production interruptions and eliminate surprise material shortages with Genius Inventory Management. Order stock and replenish parts based on actual on-the-job demand or for inventory. You can also use your mobile device to move material, manage inventory, and eliminate duplicate data entry.
Genius Inventory Management lets you keep tabs on your inventory down to the serial number and associate different statuses to materials—so that specific materials can be counted and allocated to a project before production even begins—meaning you will never run out of stock halfway through a job.
With Genius Inventory Management, you can also easily create inventory forecasts based on current and planned jobs and then create production schedules or purchase materials based on these estimates.
—-
Want to see how Genius ERP helped a custom manufacturer reduce their time spent on purchasing to only 25 minutes a day? Read our case study of Motrec Industries.
Get your eBook Scared to implement a new ERP?
"*" indicates required fields