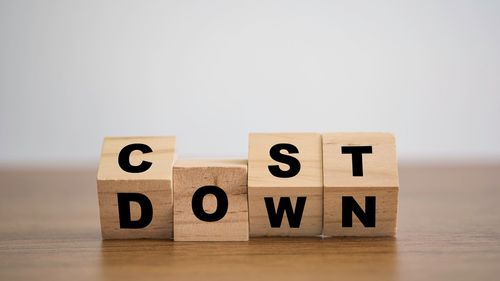
ERP implementation projects are expensive — and often contain unforeseen costs that you didn’t have in your budget. Even the best-planned projects are bound to encounter a few unexpected hiccups along the way. Read on to learn about the three most common hidden or unforeseen costs of ERP implementation — plus what you can do to save on these costs.
1. Training Costs
Training costs are probably the most overlooked area when it comes to ERP implementations.
Training is one of the most critical aspects of the implementation process for manufacturers. It will give your staff a chance to learn and use the system properly — getting everyone in your organization ready for the launch of the new system.
But, estimating training costs is difficult.
Some people within your organization will need little training. Either their job processes will change very little under the new system, or they are naturally fast learners and quick to pick up the system.
Others in your organization, however, will require extensive training. For some, all of their daily tasks and processes will change, meaning they will need extra time to learn the new system and their new job duties. You will also probably have some staff members who are less comfortable with technology or just need a little extra time to become thoroughly familiar with the new ERP system.
Investing in quality training is essential.
Many ERP implementations fail because companies are unwilling to invest the time and energy needed into the amount of training that is required to get a new and complicated system up and running. While it may seem like a savings to cut some corners when it comes to training, you are doing the complete opposite — as the expensive ERP software system you invested in isn’t being used properly, and you are not reaping the rewards you should be from your ERP.
Trust us when we say it will be cheaper for you, in the long run, to ensure that everyone is using the system properly from the start. Experienced ERP training consultants can be expensive, but it is worth it to have knowledgeable people who can help you learn, understand, and use your new system.
ERP projects can also take over a year to fully implement(!). You will most likely have some staff turnover during that time, which means that you will also need to invest additional time and money into training new hires to get them up-to-speed on the system.
This adds up to more money spent on training than you may have initially budgeted. No one likes cost overruns, but taking the time to invest in and properly train your staff is one of the most important components of an ERP implementation project — and one that will pay off for your organization in the long run.
2. Re-engineered Processes
Evaluating your business processes and identifying pain points is an important step of the ERP selection process — yet many manufacturers will try to complete their implementation in the shortest time with the least amount of changes required, skipping this crucial step.
The truth is that none of us have fully optimized processes — inefficient processes were probably one of the reasons you decided to get a new ERP in the first place.
Your new ERP will have best practices built into it, so it only makes sense that you take the time to re-think and revise your processes to match these best practices. Utilizing the built-in best practices makes much more sense than paying to customize your new ERP system to continue using inefficient processes.
When used properly, ERPs are robust tools that can save you time and money and help your entire company — from back-office operations to the shop floor — run more efficiently and effectively. But to get full advantage of your ERP system, you need to use it in conjunction with better processes.
Don’t remove process re-engineering from your ERP implementation project.
Take advantage of the opportunity an ERP implementation project affords you — your employees already need to make changes and adapt to a new system, so ask them to adopt better processes at the same time. You’ll find re-engineering a process is a lot cheaper than the alternative, which involves tailoring your new ERP system to adapt to outdated and inefficient company processes. It will also result in a more efficient workplace.
Taking time to create newer, better processes — or hiring an ERP or manufacturing consultant to help you — can be costly. However, like with most things in life, if you take the time to do things right from the start, you will be rewarded with a more effective and efficient shop.
3. Employee Resistance to Change
I know we sound like a broken record on this front, but ERP implementations are disruptive!
Naturally, any system that affects so many areas of your organization will bring a lot of change to your shop, which can be difficult for many people to adapt to. Some within your organization will be excited about the new system and will foresee the positive effects the system will bring your business. But others will be reluctant and resistant to the change and disruption the new ERP brings to their daily work tasks. If you do not have an effective change management plan in place, these employees may hinder or even sabotage your efforts to implement the new system.
Getting key users and stakeholders within your company on board with the new system from the very beginning is crucial. If you know how important the operations manager will be to the ERP implementation process, get her involved right from the start of the project. Make sure she understands the importance of the new system to your business and that she is an integral participant in the project. This way, instead of being someone who can delay and derail the implementation process, she is an ally and a partner and will help you to get other people on board.
Establish a strategy for managing change.
You may also consider adding a change management specialist to your implementation team. Change management specialists have very specialized training related to organizational change. They will help you differentiate between — and will provide you with strategies to help — those who can easily deal with change, from those staff members who need a lot of handholding to get past their reluctance.
A change management specialist may be another additional cost that was not initially in the budget. Still, like with everything else on this list, if you address problems and issues at the beginning of your implementation project, you will be better off.
Want to save on ERP implementation costs?
I don’t want the above list to scare you off from an ERP implementation project. ERPs are life-changing to your manufacturing shop, and anything that brings so much change is bound to have some unforeseen costs and glitches — but getting a new system in place is worth the disruption.
RELATED ARTICLE: The Do’s and Don’ts of ERP Implementation From an ERP Expert
Like with any large project, the more upfront planning you do, the faster and smoother the implementation process will go — saving you money. You may be reluctant to build extra time and money into your budget for training and change management, but if you do so from the start, things will go smoother, your ERP implementation won’t get derailed, and in the long run, you will save money.
Make certain you have an internal champion for your ERP project.
A strong internal champion for your implementation project takes on the ins and outs of the ERP implementation process — and can help overcome internal resistance to change, whether or not you hire a change management consultant.
The person in this position must balance having a great deal of authority and influence inside the organization with being friendly, approachable, and open to others. Your champion must be someone who has the power to escalate issues and get them fixed fast — but also someone your staff feels comfortable approaching with their problems and concerns.
A good internal champion will go a long way to helping your implementation project stay on track and ensuring tasks like process re-engineering get completed on time.
Consider a phased approach.
Instead of changing all your business processes at once (remember hidden cost #2?), you can tackle your most problematic area first — changing those processes and only implementing the specific ERP modules that address that problem. Continue to break down the project into phases, implementing pieces of your ERP system at a time.
This strategy is particularly effective for small manufacturing shops with more modest budgets for an ERP project. Through a phased approach, you improve what you need to most, plus eventually get a complete manufacturing-specific ERP system at a price, and on a timeline, that works for you.
Be open to new types of training.
Training is one of the most critical but also most expensive elements of an ERP project. But there are ways to keep costs down.
Look for an ERP vendor that has alternatives to costly on-site training days. While having a consultant on-site from time to time is extremely helpful during the implementation process, consider using e-learning platforms to train your staff. Online training resources allow your staff members to get up-to-speed at a pace that is right for them. Staff members who need extra training can do so on their own time, and not hold back the entire project and monopolize consultants’ time. Built-in tools will allow you to track your team’s readiness with quizzes and performance metrics.
Online training programs can guide teams through every step of the implementation process, from kick-off to go-live. Training — through e-learning modules, videos, virtual classes, and more — is personalized for each role within the organization and allows manufacturers to reduce the need for costly consultants. You will get all the instruction and preparation you need to launch a new system, but at a considerably lower price than traditional in-person training.
———
If you want to implement a new ERP system but are looking for ways to reduce costs, check out Genius Academy. Our industry-leading online training platform is easy-to-use and accessible. We give you all the tools and resources you need to get up-to-speed with Genius ERP, but at a price that is right. Visit Genius Academy to learn more.
Get your eBook Scared to implement a new ERP?
"*" indicates required fields