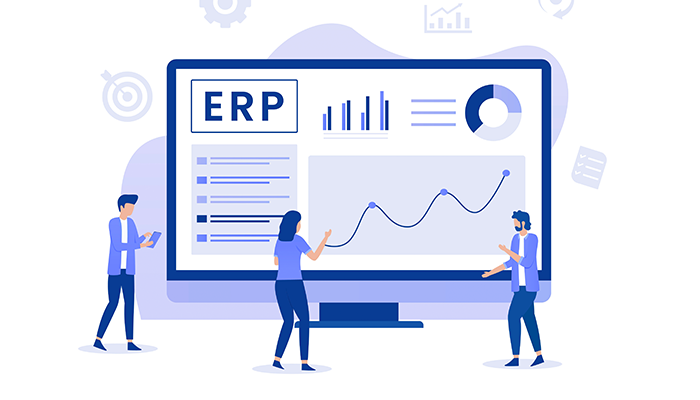
Table of Contents:
- What is an ERP?
- Generic ERP Systems vs Manufacturing ERP Systems
- Top ERP Modules for Manufacturers
- Benefits of a Manufacturing ERP
- ERPs for Different Types of Manufacturers
- How To Select the Right Manufacturing ERP for You
- Final Thoughts
With so many enterprise resource planning (ERP) solutions available and boasting diverse features and functionalities, finding the best fit for your unique manufacturing needs can be difficult. To help you understand more about manufacturing ERPs, why they are indispensable in today’s manufacturing landscape, and how to find the best manufacturing ERP for you, we have broken down the key features and functionalities you should know about.
From streamlining production processes to optimizing supply chain management, a robust manufacturing ERP should offer comprehensive tools tailored to enhance efficiency and competitiveness. Our guide aims to provide valuable insights and practical guidance, helping you to make the best decision and find the right manufacturing ERP that aligns seamlessly with your specific requirements.
What Is an ERP?
An ERP is process management software that connects and integrates every aspect of a business. ERPs give manufacturers visibility over their entire operation, allowing them to create better manufacturing processes, lower costs, and improve performance.
A manufacturing ERP system integrates your financials, supply chain, operations, reporting, and manufacturing activities into one system to improve performance and productivity. Without an ERP system, manufacturers must use multiple software programs and systems, like Excel, that are not integrated. This results in poor performance by slowing down collaboration and limiting efficiency.
Manufacturing ERPs
Manufacturing ERPs serve as the backbone of your business, interconnecting all business processes and facilitating seamless data flow. Instead of several standalone databases and an endless amount of disconnected spreadsheets, ERP systems allow all users — from the CEO to shop-floor employees — to create, store, and use the same data.
ERPs have closely monitored access points and user permissions — reducing your susceptibility to human error and stopping people from accidentally accessing and changing data — to ensure that you always have accurate, trusted, and safe data.
ERPs eliminate data duplication (saving time and money and reducing errors) and give you data integrity, resulting in a reliable, accurate, and secure data environment.
But beyond basic data management, modern manufacturing ERPs go a step further, offering a diverse array of tools and functionalities tailored to meet the unique challenges of your industry. Modern ERP solutions include manufacturing, supply chain management, and financial and accounting capabilities, but can also have advanced reporting and business intelligence, sales force and marketing automation, CRM management, and project management functionalities.
Manufacturing ERPs link every department in your organization, including finance, purchasing, engineering, and operations, by connecting both the systems and the people who use them.
Simply put, a manufacturing ERP is the best solution for integrating people, processes, and technologies across a business — the advantages of which are almost endless.
Generic ERP Systems vs Manufacturing ERP Systems
Generic ERP Systems
Many of the biggest, well-known ERP systems are generic or generalist ERPs. Generic ERPs are very robust systems that offer a wide range of features and functionalities. Generic ERP systems can adapt to processes used by companies across various industries but require customizations and add-ons to do so.
Manufacturing ERP Systems
Manufacturing ERP systems are designed to meet the needs of the manufacturing industry. They are often developed by smaller, niche companies that are made up of a team of industry experts with the sole focus of solving the distinctive needs of manufacturers. Manufacturing ERP systems include the same features as generic systems — accounting, finance, inventory management, project management, etc. — but will also have features that target the unique needs of manufacturers.
An ERP system designed for the manufacturing industry will include an MRP (Materials Requirement Planning) module, along with other customized features that manufacturers need. Manufacturing-specific ERP systems are out-of-the-box ready as they do not require customizations to create industry-specific features and capabilities.
Manufacturing ERPs have greater, more tailored capabilities because they have been designed with a deep understanding of industry-specific processes. In addition to the shorter implementation timeline, reduced implementation costs, and lower system maintenance fees, manufacturing ERPs can offer a higher level of functionality at a lower price point. These systems offer standard features and capabilities tailored to your industry and operational needs that generic ERP systems simply can’t provide.
Along with the basics like accounting, business intelligence, and inventory management, manufacturing-specific ERPs will include features specific to manufacturers, like product engineering, quoting and estimating, job costing, and shop-floor scheduling.
Top ERP Modules for Manufacturers
ERPs are integrated systems that run off of a central database — in real-time — to manage all of your business processes. Functionally, they are broken down into different applications, or modules, each with a unique set of tools focused on a different set of business processes. For example, some common ERP modules are accounting, inventory management, human resources management, and purchasing.
While all the modules will have a consistent look and feel about them, each individual module will include the specific functionalities required to address a particular business need. For example, an ERP accounting module will consist of a full-suite accounting software package.
The beauty of an ERP solution is that not only will each of your departments have access to best-in-class software tailored to their specific needs, but also — because the modules are grounded within the same system — information can flow freely between modules, connecting your entire organization.
Real-time data and connectivity facilitate information flow between all business functions, improve your shop’s performance, and allow you to make better, more informed decisions about your business.
Materials Requirement Planning (MRP) Module
MRP stands for Material Requirements Planning and is a software solution that helps you precisely calculate what materials you require, when, and in what quantities.
Modern ERP systems grew out of MRPs, but MRPs are still a valuable tool for manufacturers. MRPs give you control over your manufacturing processes and include powerful tools to help you with production scheduling, managing bills of materials and inventory, machine capacity scheduling, demand forecasting, and quality assurance.
Including an MRP module within an ERP system offers enhanced production efficiency, streamlined inventory management, and optimized resource utilization, ultimately contributing to cost savings and improved overall operational effectiveness.
Inventory Management Module
An integrated inventory management module will let you track your inventory needs, control your costs, and replenish stock based on actual demand.
ERP inventory management software lets you keep tabs on your inventory down to the serial number. For every item in your inventory, you will always know how many are reserved for a job, how many are available, how many are currently in production, and how many are on order — to avoid production interruptions and eliminate surprise material shortages.
Good ERP inventory management systems will also include multi-warehouse and multi-location functions, letting you keep track of inventory across your operation, no matter how many locations you have.
Supply Chain Management Module
ERP supply chain management lets you manage your supplier and vendor relationships in a system that is synced with all of your projects and your inventory. This allows you to improve relationships with your vendors, streamline purchasing processes, and ensure that you always have the right materials on hand.
Manufacturing ERP systems let you manage all your interactions with vendors in a single system — including quote requests, purchase orders, receiving, and invoicing — to better control costs. You can quickly evaluate vendors on several factors like on-time delivery, quality, and price, guaranteeing that you always choose the right supplier for every job (and ensuring raw materials are always on hand).
CAD2BOM Module
Do you know that up to 20% of the total engineering time in your shop is taken up by transferring Bills of Materials (BOMs) out of your CAD system into an ERP? A CAD2BOM module will seamlessly export a BOM from your CAD system into your manufacturing ERP, creating a fully itemized list of the materials ready for procurement and production.
A good manufacturing ERP system should offer full automation, allowing seamless data transfer between your CAD system and ERP at the touch of a button. This eliminates redundant data entry and provides the capability to automatically reconcile and fix errors. It’s also crucial that any edits made in the CAD system automatically update in the ERP system.
Finance and Accounting Module
Good manufacturing ERP systems will include a full-featured, multi-company, multi-currency accounting and financial management system that is easy to use — and ensures that your accounting department is in sync with the rest of your business.
Real-time data and fully customizable dashboards allow you to easily manage your accounting and financial management operations from one place. Using a single system that is fully integrated from quote to payment eliminates the need to operate and maintain parallel systems. With all financials in a single database, accounting staff won’t spend hours manually cross-referencing, re-entering, or reconciling data — and will have more time to focus on delivering critical reports and other vital tasks.
Shop Floor Management Module
Connect your shop floor to the rest of your operation with a manufacturing ERP to make informed decisions that drive efficiency and productivity. Gain a complete view of your processes with a connected production floor to maximize your shop’s coordination and collaboration.
An integrated shop floor management system tracks data and production progress and brings your operations together to give you complete visibility of your shop floor. Real-time data creates instant alignment between management decisions and shop floor priorities. Empower shop floor employees to access task lists, track work time, locate work-in-progress (WIP), and embrace a paperless work environment with a manufacturing ERP system equipped with shop floor management features.
Customer Relationship Management (CRM) Module
A CRM is an indispensable tool for managing the sales process for manufacturers.
CRM modules incorporate many features that make managing the selling process easier, including a personalized sales dashboard for handling customer information, leads, and opportunities, as well as marketing automation tools to create marketing campaigns and mass emails. A CRM is also a valuable tool for managing the relationship you have with your current customers. More information about your customers can help you communicate more regularly and effectively with them, which will lead to a stronger relationship — and increased loyalty.
Job Costing Module
The process of tracking and assigning costs is almost impossible for manufacturers to do without an integrated manufacturing ERP system. Manufacturing ERPs with integrated job costing automatically monitor and analyze costs associated with individual operations, projects and jobs in real time to give manufacturers precise job cost calculations.
Accurate job costing is vital as it determines the actual cost of a job and helps you set the right price for your customers and improve efficiency. With a good manufacturing ERP, you will be able to compare estimated to actual costs and determine which of your jobs are truly profitable and which customers you should go after.
Benefits of a Manufacturing ERP System
Manufacturing ERPs are the industry gold standard for a reason — nothing streamlines business processes, provides accurate real-time data, and reduces costs better than an ERP system. Below are some of the top benefits of an ERP system for manufacturers.
Real-Time Data
Real-time data has revolutionized the manufacturing industry by changing how shops are managed and goods are manufactured.
Real-time data provided by manufacturing ERPs lets you know which of your production processes, machines, work centers, and product lines are operating at high levels of quality and efficiency — and which aren’t — which allows you to make changes quickly and fix any issues before they get out of hand.
Real-time data lets you continually track, control, and fine-tune your shop for maximum efficiency. With it, you can oversee your shop floor schedule, consistently improve product quality, and maintain your equipment to create a higher-performing manufacturing plant.
Improved Efficiency
Manufacturing ERPs help increase your shop’s efficiency by streamlining your business processes.
Take a look at Motrec International. Before they used Genius ERP for inventory management, they would close down for three days and spend $400,000 on taking their inventory. With Genius ERP, they now use the automatic and integrated cycle count for their inventory, saving them hundreds of thousands of dollars, increasing the accuracy of their inventory, lowering the amount of stock on hand, and reducing the time spent on purchasing.
ERPs streamline your tasks and business processes so you can do things faster, better, and more consistently.
Enhanced Collaboration
Using one integrated system across your organization — from accounting to engineering to production to shipping — will increase collaboration across your shop
All your staff can work off of the same centralized shared database, making it easy to share accurate data and information between departments. Manufacturing ERPs break down information silos to create a more open, transparent, and collaborative workplace.
Reduced Costs
Manufacturing ERPs reduce operational and administrative costs because they help you better manage every aspect of your shop. From labor costs to supply chain management to your engineering department, an ERP will make you more efficient, lowering your operational costs. For example, ERPs can help you better manage things like long-lead items to prevent costly production delays.
Above, we saw how Motrec International saved $400,00 on inventory management costs alone when they started using Genius ERP to track inventory. A recent study by the Aberdeen Group found that an ERP solution could reduce operational costs by 23%, reduce administration costs by 22% and increase on-time deliveries by 24%.
Better Business Decisions
We could write a whole blog post on this topic — in fact, we’ve written more than one — as there is so much to say about how ERPs give you improved business analytics.
In the past, manufacturers needed to comb through numerous spreadsheets and systems to pull out relevant data and then analyze the data to create meaningful reports. Now, the right manufacturing ERP will not only house all of your data in one place but will have built-in business intelligence (BI) tools to analyze data and create powerful reports to help you become more effective and productive — and make better decisions about your manufacturing business.
ERPs for Different Types of Manufacturers
No matter the type of manufacturing you do, an ERP is the best way to boost productivity in your shop.
ERPs improve your operations by combining your data and processes into one system and give you an integrated tool to help you optimize resources and enhance decision-making. ERPs, for a start, assist your business in streamlining financial processes, managing schedules, reducing errors, simplifying production planning, ensuring timely communication and collaboration throughout your organization, and so much more.
Engineer-to-Order (ETO) Manufacturing
Engineer-to-Order (ETO) manufacturing is synonymous with customization. In this type of manufacturing, products are designed and engineered according to individual customer specifications. Whether it’s a complex industrial machine or a precisely engineered component, ETO manufacturers craft unique solutions. Each project starts with a blank canvas, demanding intricate design, engineering and planning. As a result, lead times can be lengthy, costs higher, and supply chain complexity intensified.
An ERP system is essential as it integrates data from various departments, enabling seamless collaboration between design, production and procurement. An ERP also accelerates communication, expedites design iterations and ensures timely material sourcing, making it easier for ETO manufacturers to meet customer expectations for quality and delivery.
Configure-to-Order (CTO) Manufacturing
Configure-to-Order (CTO) manufacturing strikes a balance between customization and efficiency. Manufacturers offer pre-configured options that customers can choose from to create a tailored product. This approach reduces lead times compared to ETO, as manufacturers work within predefined configurations and components.
ERPs help in CTO scenarios by managing product configurations, optimizing inventory levels and generating accurate bills of materials based on selected options. This streamlines production, ensuring that customized products are assembled swiftly and accurately.
Make-to-Order (MTO) Manufacturing
Make-to-Order (MTO) manufacturing is about producing products as soon as an order is received. Unlike ETO, MTO manufacturers rely on standardized designs but still only initiate production once an order is confirmed. This approach ensures alignment with market demands and minimizes excess inventory.
An ERP system is vital for MTO operations, coordinating production schedules, procuring necessary materials and tracking orders from inception to delivery. An ERP helps MTO manufacturers to be more agile, avoid overproduction, and maximize resource utilization.
Make-to-Stock (MTS) Manufacturing
Make-to-Stock (MTS) manufacturing centers on producing goods based on forecasted demand to build inventory in advance. This strategy suits products with consistent demand patterns and shorter lead times.
ERPs provide real-time insights into inventory levels, sales trends and demand forecasting, enabling MTS manufacturers to strike a balance between maintaining the right inventory level and avoiding overstocking. This data-driven approach helps prevent stockouts while minimizing holding costs.
Contract Manufacturing
Contract manufacturing refers to a business arrangement where one company, the contract manufacturer, produces goods or components on behalf of another company. Contract manufacturing jobs can range from producing simple components to assembling complex products.
ERPs foster collaboration between the client and contract manufacturers by integrating processes and data, which ensures that product specifications, quality standards and delivery expectations are met seamlessly. ERPs also help contract manufacturers manage multiple orders, letting them efficiently process orders, track their status and address changes.
How To Select the Right Manufacturing ERP for You
The first step in finding the right ERP system for you is to identify why you need an ERP in the first place. Before you start researching different ERPs and their features, costs, implementation methods, and other factors that, don’t get me wrong, will be important to finding the right ERP system for your business, take a step back and figure out why you need an ERP.
The obvious answer is that if you want to grow your business and remain competitive, and you need a comprehensive manufacturing ERP system to help you manage every aspect of your business.
But you actually need to dig a little deeper than that.
All good manufacturing ERPs will help you increase your efficiency and reduce costs. A manufacturing ERP will connect and integrate all the different aspects of your business into one database, streamline your tasks and processes, and let you share accurate information across your company. But to truly find the best ERP for you, start thinking about what your business really needs to get out of an ERP.
The next step is to identify the specific problems your manufacturing business has and how you can fix them. Sit down with a small, trusted group of people at your company and ask yourself what do we need to improve to become a better business?
A good sentence to figure this out is, “We need to improve ______ by ______.” Maybe you need to improve profitability by cutting down on raw material costs. Maybe you need to reduce errors by clarifying procedures. This isn’t an easy step, and it will take effort and work to figure out precisely what your business needs to improve, but once you have, you can almost guarantee that you will be able to find the right ERP for you.
Only once you know what your organization definitively needs to improve your business can you start looking for a manufacturing ERP system with the right features for you. Instead of becoming distracted by bells and whistles that won’t be useful to your organization, you will be able to focus on the features that will benefit your manufacturing business the most.
To learn more about how to pick the right manufacturing ERP for your business, download our eBook: How To Select the Right ERP to get the five steps you need to follow to find the right manufacturing ERP for you.
Final Thoughts
The right manufacturing ERP not only streamlines processes and enhances efficiency but also plays a key role in the overall success of your business. overall business success. Armed with the insights provided in this guide, you should now be well-equipped to find the right manufacturing ERP for your needs, ensuring that your chosen ERP becomes a valuable asset in pushing your manufacturing operations to new heights of productivity and competitiveness.
Get your eBook Scared to implement a new ERP?
"*" indicates required fields