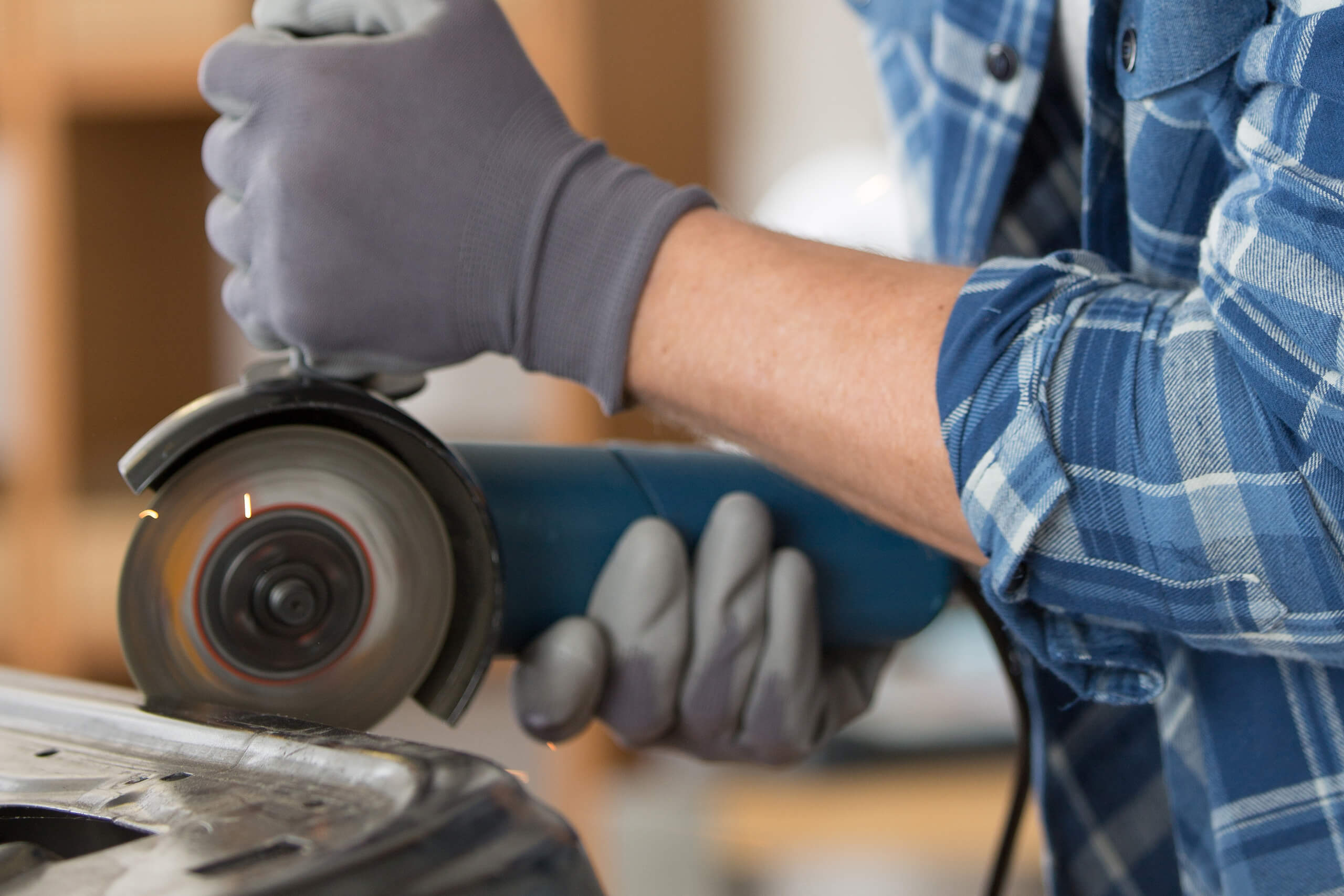
A quick definition to get us started
A buffer is used in manufacturing to adjust for variations in the production process. Think of a buffer as a way to ensure that your production line continues to run smoothly despite unforeseen factors coming into play.
One example of a buffer in manufacturing is keeping enough materials on hand as a safeguard to ensure operations run smoothly. Manufacturers will keep the raw materials and supplies needed for production, and sometimes inventories of finished products waiting for shipment, on hand to help stabilize any fluctuations they experience with their supply and demand chains, production capacities, and lead times. Without appropriate buffers in place, manufacturing processes can slow down, meaning that expenses increase and profits decrease.
A buffer is also an important concept in DBR scheduling — it’s the B in DBR afterall — and it keeps your shop running at maximum capacity. In DBR scheduling a buffer is simply defined as a period of time put in place to ensure your shop runs smoothly. Buffers protect your drum — the biggest constraint or problem that causes your shop to slow down — and make certain it is always fed, so-to-speak, and able to run at maximum capacity.
In other words, this means that your drum will never be starved for work, and that jobs will pass through to the drum at the correct pace. (Remember in DBR scheduling, your shop can only run as fast as your drum allows, so ensuring that your drum runs at maximum capacity, ensures that your entire shop runs at its maximum capacity — that’s why you need buffers in place, to guarantee that your shop always runs smoothly.)
What problems arise when you don’t have buffers in place?
Bottlenecks, bottlenecks, bottlenecks
The biggest problem that occurs if you don’t have proper buffers in place are bottlenecks. In custom manufacturing bottlenecks are — unfortunately — inevitable. The truth of the matter is that bottlenecks are simply a fact of life for custom manufacturers, because you are always building a new and unique product. Learning to understand and accept that fact — and then learning to implement buffers in your shop — will change how efficiently your shop runs.
Putting proper buffers in place will allow you to compensate for bottlenecks, and ensure that your production line always runs smoothly.
Out of control delivery dates
Accurate delivery dates are difficult for even the best custom manufacturer to calculate. Add in the strain of bottlenecks to your production line, and without buffers, your shop will inevitably deliver jobs late over and over again.
Inserting buffers into the proper places along your production line will ensure that products flow through the production system as quickly and efficiently as possible, and that excess time is eliminated from your schedule — meaning that you will always deliver finished goods on time.
Trouble with your throughput
Throughput is the most crucial measurement for your shop — but one many manufacturers get wrong: The correct definition of throughput isn’t the amount of time it takes to complete a finished good, but the rate at which the system generates money through sales. It’s important to remember that throughput is linked to sales, as making money is your business’s goal afterall.
Your throughput will inevitably slow down if you don’t have buffers in place to control your bottlenecks.
But remembering to define throughput in terms of sales will ensure that you are prioritizing your shop correctly: It’s no use putting in buffers to push jobs through your shop, if they are only going to sit on your shelf as excess inventory. You need to ensure that the jobs you are prioritizing, and the jobs that you are moving through your bottlenecks, are the jobs that you have customers waiting on.
DBR scheduling, with its use of proper buffers, is designed to maximize the throughput of your shop, by ensuring that you are setting the right priorities, and speeding up bottlenecks, to maximize profits.
How to implement buffers in your shop
Having proper buffers in place is important to stop unforeseen events from hurting your production and sales. In an ideal world, buffering wouldn’t be necessary because variability and unforeseen circumstances wouldn’t exist, but custom manufacturing isn’t an ideal world, and variability always exists. The complex nature of custom manufacturing will almost always mean that something unforeseen comes into play — meaning buffers are critical to the custom manufacturing process.
To go back to the example we used at the start of this article, keeping an inventory of raw materials on hand to use as a buffer in case of any fluctuations in terms of your supply chain will ensure that your production line keeps running, and is an easy buffer to put in place. If you didn’t have this buffer of additional materials, any hiccups along the way would make your production slow down, causing you to deliver late and put a dent in your profit margins.
To know where to place a buffer you need to be able to identify your bottlenecks. (Don’t worry, we wrote a blog on that topic giving you 5 straightforward steps to identifying bottlenecks in your shop). Once you’ve identified where the bottleneck is in your system, you can appropriately situate your buffer.
Placing A buffer before a bottleneck ensures that your bottleneck doesn’t suddenly run out of work and sit idle for too long, slowing down your entire plant. (Remember the rate of your slowest bottleneck will determine the overall capacity of your shop.)
Through buffering, manufacturers can alter their processes by manipulating inventories, capacities, and times. For example, if producing a finished product is a three-part process, and the first step takes longer than the final two, keeping a buffer inventory of completed first-step parts in-place will ensure that the second and third steps won’t experience lag times during production.
Warning: Implement buffers correctly
Placing a buffer immediately before a bottleneck ensures that your entire production line continues to run smoothly, and that you keep costs low and profits high — as long as it’s implemented correctly, that is.
Remember, you want to improve your throughput — and throughput is defined in terms of sales.
Let’s go back to our first example of having extra inventory on hand as a solution to ensure that your bottleneck is constantly fed, even in the case of a late delivery on the part of a vendor. But, having too much excess inventory on hand — either as raw materials, or finished products — can end up costing you more money, and decrease your profitability, if too much piles up on your shelves.
To maintain an optimal balance, many manufacturer’s use lean manufacturing strategies in which they learn to use the least amount of buffering necessary to ensure optimal shop capacity. (Using an ERP is also a great way to help you better manage inventory levels.)
Get your eBook Scared to implement a new ERP?
"*" indicates required fields