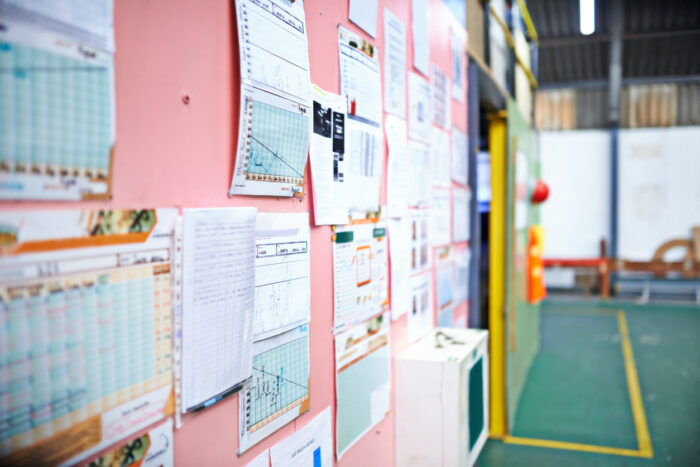
What is a production bottleneck?
A production bottleneck is a point in your production line where workloads accumulate because they arrive too quickly to be processed.
Intuitively, as an experienced manufacturer, you can probably quickly identify the bottleneck(s) in your shop—just take a minute to think about which workstation or other areas in your shop that has the longest wait times, is constantly backlogged, and causes everyone in your shop to have high stress levels—this is your bottleneck. (If you still need help on how to pinpoint the bottlenecks in your shop, check out our blog here that lays out 5 ways to easily identify the production bottlenecks that are holding you back).
Bottlenecks are problematic because they not only cause you undue stress, they actually limit the capacity of your entire shop. Bottlenecks aren’t just small kinks in the system, they are, in fact, what determine the overall output of your plant. We’ve all heard the expression ‘a chain is only as strong as its weakest link.’ That’s effectively what a bottleneck is to your shop—your production line can only go as fast as your worst bottleneck allows.
What are the primary causes of a bottleneck?
There are two types of bottlenecks: short-term bottlenecks and long-term bottlenecks. Short-term bottlenecks will crop up from time to time—think somebody is out sick for a day, causing a backlog at a work center—and will resolve themselves quickly when things get back to normal. Short-term bottlenecks are a normal part of the manufacturing process and are something you don’t need to worry about.
Long-term bottlenecks, on the other hand, can cause major disruption to your production, and if they aren’t addressed properly can cause major delays, and even grind your operations to a halt.
Long-term bottlenecks that custom manufacturers experience can include things like: a machine is not efficient enough and as a result has a long queue; an assembly is routinely waiting for long-lead items before proceeding; engineering takes upwards of a week to turn designs into an actionable MRP file; or a backlog builds up between two work centers (requiring wasted work-hours, as well as issues with storage and moving work-in-process items).
Long-term bottlenecks can be the result of poor planning and scheduling, outdated equipment, improper maintenance schedules causing machinery breakdowns, worker shortage, or bad forecasting.
Unfortunately, the very nature of custom manufacturing can also make long-term bottlenecks more prevalent. On top of proper maintenance schedules, updating equipment, and other factors all manufacturers need to account for, custom manufacturers are always designing and building new products that haven’t been made before, making effective planning and scheduling extremely difficult, as there are so many variables that custom manufacturers need to deal with giving custom manufacturers challenges that can easily turn into bottlenecks. For example, knowing which long-lead items need to be purchased is a challenge, as these items need to be procured early in the process, before product designs are even finalized. (ERPs can be a major benefit to help custom manufacturers with procurement of long-lead items. Learn more here).
Fortunately, there is a planning and scheduling system, called DBR, or Drum-Buffer-Rope, that can help custom manufacturers better manage and deal with bottlenecks.
What is Drum-Buffer-Rope scheduling?
DBR is a scheduling tool that is derived from the Theory of Constraints (ToC), and requires you to think about how you schedule your shop in a completely different way. The underlying principle of DBR scheduling is that within any manufacturing shop there is a drum—one, or a limited number of scarce resources (i.e. a bottleneck)—which controls the overall output of the shop. The performance of the system’s drum, or bottleneck, will determine the performance of the system as a whole.
Traditional scheduling systems rely on consistent data fed into an algorithm to create a schedule for your shop. The problem custom manufacturers face is that they don’t have this consistent data (because they are always building new, custom products), meaning they rely on estimates and educated guesses. But what this translates into is that schedules created by traditional scheduling systems are not able to be accurate, because they are not built from accurate data.
DBR scheduling throws this way of creating schedules out.
The point of a DBR scheduling system is to maximize your shop’s capacity by maximizing the output of your bottleneck. Therefore DBR scheduling systems create a schedule built around your bottleneck and how your shop actually functions—not data points—to create a schedule that will work for you, and ensure your shop is running as efficiently as possible. A DBR scheduling system automatically prepares a detailed schedule that maximizes the capacity of the drum. And then the system automatically puts buffers and ropes in place, which are mechanisms that ensure the drum always operates at maximum efficiency.
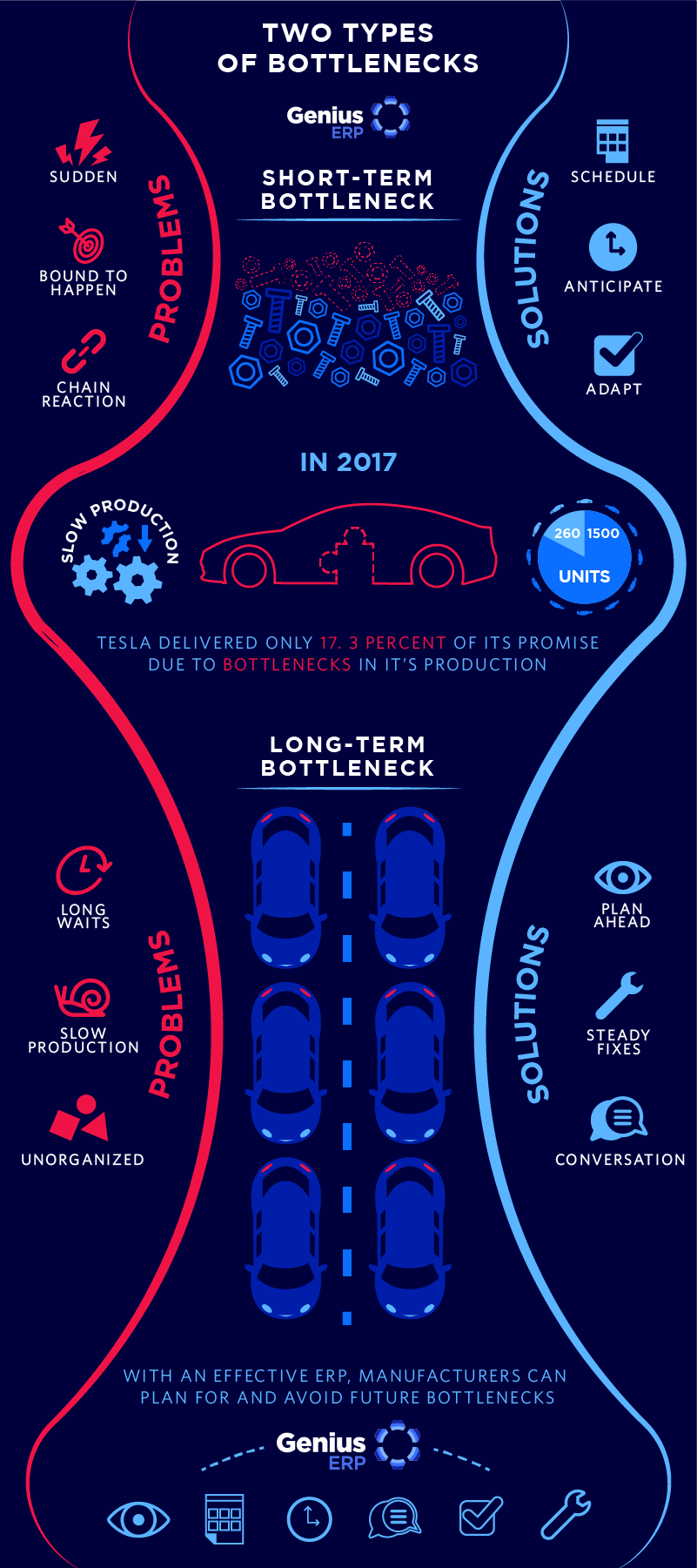
How can DBR mitigate, and help solve bottleneck pains?
DBR scheduling helps your shop deal with bottlenecks by acknowledging that bottlenecks are what sets the overall capacity of your shop—and then creates a schedule that maximizes the efficiency of your bottlenecks.
DBR scheduling systems, in effect, make you rethink bottlenecks. Instead of looking at a bottleneck as something that is bad, and needs to be eliminated, you need to accept that bottlenecks are simply a fact of (manufacturing) life. Because of the complex nature of a custom manufacturing plant, there will always be a work center or resource in your plant that is going to be a bottleneck.
Learning to understand and accept that—and then learning to schedule your shop around your bottleneck—will change how you think about scheduling, and how efficiently your shop runs. As a custom manufacturer you can’t eliminate all long-term bottlenecks, but you can address them, and learn to lessen their impact by creating the proper schedule for your shop.
To learn more about DBR scheduling and how it can help you overcome bottlenecks read our articles on What is DBR Scheduling and The Advantages of DBR Scheduling. And don’t forget to check out Genius ERP’s Smart Scheduling, the only DBR scheduling system available to custom manufacturers within an ERP.
Get your eBook Scared to implement a new ERP?
"*" indicates required fields