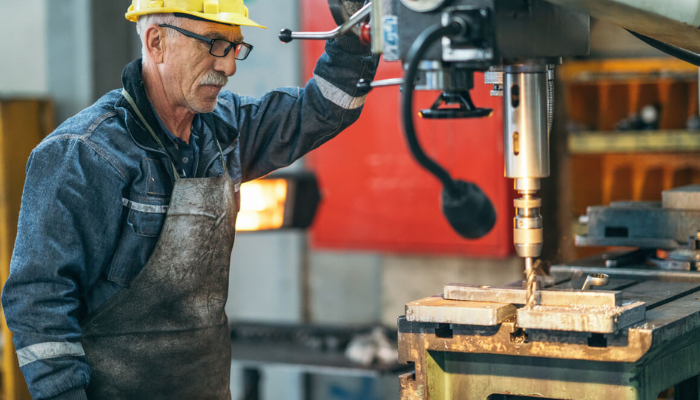
All manufacturers, unfortunately, have to deal with bottlenecks at some point. Bottlenecks can effectively grind your operations to a halt, causing you to deliver orders late—and even cost you business altogether. With the complicated nature of custom manufacturing, it’s no surprise that bottlenecks appear, causing what was once a smooth-running operation to become slow, inefficient, and backlogged.
What Is a Process Bottleneck?
A bottleneck refers to any point in the production process where the flow of materials or tasks is constrained, slowing down the overall rate of production. This can occur due to various reasons, such as equipment breakdowns, insufficient capacity, inefficient processes, or resource shortages.
Bottlenecks often lead to delays, increased lead times, and reduced productivity, impacting the efficiency and profitability of your manufacturing operation. Identifying and addressing bottlenecks is crucial for optimizing production processes and maintaining a smooth workflow, ultimately ensuring timely delivery of goods to customers.
Bottlenecks come in two forms: Short-term bottlenecks and long-term bottlenecks. Short-term bottlenecks are temporary and will remedy themselves when things get back to normal. For this reason, short-term bottlenecks—when uncompounded—are not usually a significant problem. They are business-as-usual and will usually sort themselves out on their own. A couple of examples of short-term bottlenecks that manufacturers face all the time are a key technician or welder taking a vacation or a supplier missing an order by a week.
Long-term bottlenecks are a different story, though, and can grind your operations to a halt. These are delays and backlogs that occur regularly and are constantly interrupting your operations and causing slow-downs throughout your shop floor. Long-term bottlenecks can be things like an inefficient machine leading to lengthy queues, frequent delays in assembly due to long lead items, or a recurring surplus of supplies accumulating between two specific nodes (requiring wasted work hours and space to store and move WIP items).
Failing to address these types of bottlenecks can lead to a dramatic decline in your shop’s productivity, perpetuating a chaotic cycle of constantly playing catch-up and struggling to fulfill urgent orders on time.
How To Identify Bottlenecks
To fix this situation and ensure the smooth operation of your shop, you need to pinpoint the bottleneck and understand its root cause. Below are five strategies that will help you find your bottleneck:
1. Map Your Processes
Lay out your manufacturing process in a flow chart and identify each node along your process to discover where the problem is. This can be a time-consuming task, but one that is very beneficial to a busy custom manufacturing shop. Too many shops—just trying to keep their heads above water—never really map out their processes.
Plus, all too often, shops are using cobbled-together processes and workarounds developed on the fly rather than a logical and methodical well-developed process. Taking the time to really dig into your processes and how your shop gets the job done will help you identify bottleneck(s) and give you a chance to implement more efficient and effective processes to boot.
2. Look for Accumulations
This is the opposite of the above method: Take a quick minute to think about which workstation or other area in your organization has long wait times, is constantly backlogged, and causes everyone in your shop to have high stress levels.
Probably didn’t take you too long to come up with the answer, right? That workstation, process, long-lead item—or whatever it is that is always causing everyone in your plant to stress—is your bottleneck, and you need to learn how to adjust your shop’s priorities around it.
3. Adjust Throughput
The throughput of your production line is directly linked to the output of your bottleneck. Increasing throughput to a work center or resource that isn’t a bottleneck won’t do anything to increase your shop’s overall efficiency, as everything will just pile up at the bottleneck.
Experimenting where an increase in throughput actually increases your overall throughput will let you know where your bottleneck is: If you change the throughput of each of your machines one at a time, the machine that affects the overall output the most is your bottleneck.
4. Adjust Capacity Levels
Like most shops, you are probably tracking, at least to some degree, the percentage utilization of each production unit. The machine that uses the highest percentage of its capacity is the bottleneck. Usually, this machine is running at full capacity while it operates as a bottleneck and limits the other production units to a lower capacity utilization rate.
Again, like in the previous method, If you increase the capacity of the bottleneck machine, the capacity of the entire production line increases.
5. Ask Yourself 5 Whys
To find the root cause of a bottleneck, ask ‘why’ 5 times—each time drilling down to the next level to figure out what is truly causing your bottleneck. For example, if a job that you were on track to deliver on time was delayed, ask yourself why: Was it a supplier issue? An issue with a long-lead item? A work center that suddenly was backed up?
After you have identified the initial issue, continue to delve deeper. Through this systematic approach, you will soon uncover the root cause, pinpointing precisely where and why the bottleneck is occurring.
Now What?
Now that you have identified your bottleneck—no easy task—it’s time to adjust your processes to ensure that you stop the bottleneck and get your shop back up and running at maximum capacity.
I’m going to let you in on a little secret, though: The complex nature of custom manufacturing means that there will always be a work center or resource in your plant that is going to be a bottleneck. Learning to understand and accept this fact—and then learning to adjust your processes around your bottleneck—will change how you think about scheduling your shop and will boost your shop’s efficiency and productivity.
By doing the hard work to identify the bottleneck, you can learn to balance your priorities and prioritize your bottleneck to ensure that you are always running at maximum capacity.
How To Use DBR Scheduling To Overcome Bottlenecks
Whether you like it or not, bottlenecks set the speed at which your plant can produce manufactured goods, meaning that you need to schedule your shop around your bottleneck. The good news is there is a scheduling model called DBR, or Drum-Buffer-Rope, that does just that by creating a schedule around your bottleneck.
RELATED ARTICLE: A Beginner’s Guide to Manufacturing ERPs
Instead of building a schedule based off of guesswork, with DBR scheduling, your schedule is developed around—and built to support—the resource in your shop that slows you down. Within a shop that uses a DBR schedule, the constraint, or bottleneck, receives top priority in terms of repairs, maintenance, and setups, so you won’t have unexpected equipment downtime.
To learn more about DBR scheduling, check out our post here, or learn more about Genius ERP’s Smart Scheduling—the only true Drum-Buffer-Rope scheduling system available to custom manufacturers within an ERP.
Get your eBook Scared to implement a new ERP?
"*" indicates required fields